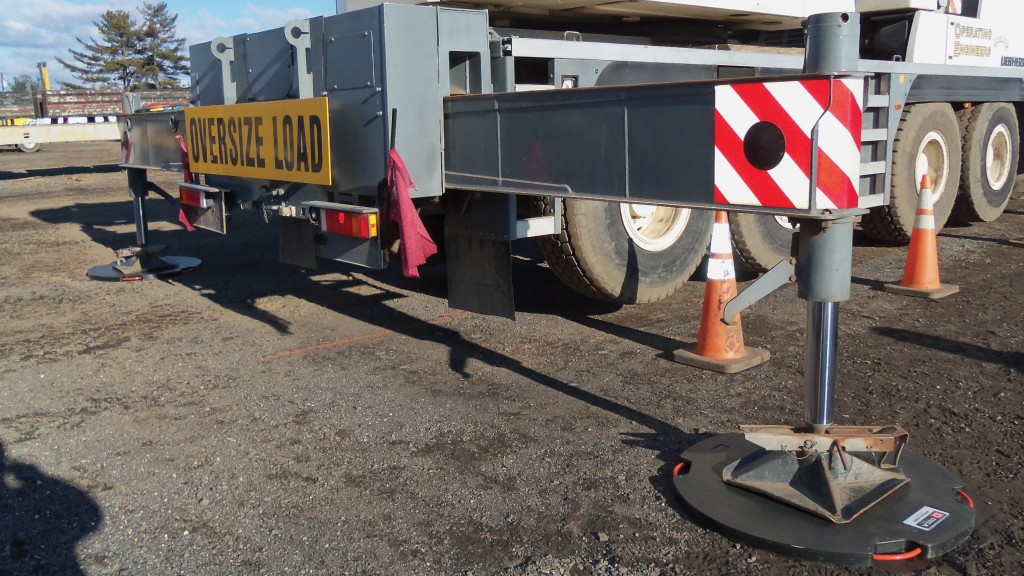
Understanding the ground conditions of the supporting surface before setting up a crane or other equipment with outriggers is essential. This includes a combination of ground bearing capacity and an understanding of suitable set-up areas, limitations, and hazards that would affect the support of the equipment into the job site, during operations, and out of the job site.
The ground bearing capacity is defined by the supporting surface's ability to withstand the forces that the equipment will apply. The responsibility for the ground and its capability and suitability to support equipment is assigned to the controlling entity for the project by OSHA 1926.1402(c)(1).* If there is no controlling entity for the project, the responsibility for providing adequate ground conditions rests on the employer that has authority at the site to make or arrange for ground preparations.
Whether you are the contractor responsible for the site or the operator communicating with the controlling entity about ground conditions and set-up needs, understanding the factors that affect safe equipment set-up is essential for safe and successful operations.
What contractors need to know
The controlling entity must supply the contractor with the permissible ground-bearing pressure for every set-up location. If any uncertainties arise, it's important for contractors to initiate a dialogue about the permissible ground-bearing pressure and to understand the extent of the controlling entity's knowledge and acknowledgment of their duties. Should the controlling entity be unfamiliar with its obligations, the contractor is advised to direct them toward the relevant regulations for clarification.
Equipment operators should perform their own visual site evaluations. Visual inspections should be focused on any presence of standing water, excavations, and indicators of underground structures such as manhole lids, utility access points, and catch basins. The intent is to ensure that all observable conditions match the information given by the controlling entity. If inconsistencies or contradictions are found, they should be immediately discussed and reconciled before operations begin.
Key terms to know
To aid in these important communications about ground conditions, here are two of the most important terms to know.
Ultimate Ground Bearing Capacity is the maximum amount of vertical pressure the ground can withstand before failing. This value must be determined by a civil engineer, who is trained and experienced in the science of determining the strength and stiffness of the ground.
Allowable Ground Bearing Pressure (AGBP) is to be specified by the controlling entity to help ensure pressures imposed on the ground stay below the levels the ground is able to support. The AGBP is calculated by dividing the Ultimate Ground Bearing Capacity by a factor of safety. The generally accepted factor of safety for temporary loading is two.
Best practices to determine ground bearing capacity
When planning to operate equipment at a site, knowing just how much weight the ground can support can be a challenging question to answer. Methods used to identify and understand the ground bearing capacity include a geotechnical report, previously documented information, and in-the-field testing and observations. A report from a geotechnical engineer will provide ground classification information and provide detailed ultimate ground bearing capacity data on the site.
In the field, physical assessments, such as plate or roll tests, and performing a visual inspection can be helpful to assess the current state. However, they should only serve as a substitute of last resort. These investigations should help operators determine if the ground should be improved, if the equipment needs to be relocated, and what type of supporting materials, such as outrigger pads, mats, dunnage, or cribbing, is needed.
DICA offers a resource page, Determining Your Ground Bearing Capacity, to help clarify some of the terms discussed in this article. A Ground Bearing Capacity Chart is included to aid in the difference between the ultimate ground bearing capacity of the supporting surface and the allowable ground bearing capacity that is used for operational purposes.
Supporting materials
There are many choices of supporting materials. Fundamentally the basic area sizing evaluation is the same for all. To determine the minimum pad area, you must know the outrigger load, also known as the Outrigger Reaction Force, and the Allowable Ground Bearing Pressure (AGBP).
The Outrigger Reaction Force is the amount of load a crane will apply to the supporting surface during operations (typically expressed as a unit of weight, such as pounds). To calculate the supporting material minimum bearing area, divide the Outrigger Reaction Force (ORF) by the Allowable Ground Bearing Pressure (AGBP); (ORF/ABGP = Pad Area).
Supporting material area calculation example
Equipment Outrigger Reaction Force = 100,000 lbs.
Allowable Ground Bearing Pressure = 3,500 psf.
100,000 lbs / 3,500 psf = 29 sf
In this example, supporting material with the strength to withstand the imposed 100,000 lbs. outrigger reaction force and the stiffness to distribute the load over a minimum bearing area of 29 sf. is required. Therefore, an outrigger pad such as a 6- x 5-foot (30 sf) is a viable solution. Additional information on this topic can be found on the resource page Stiffness vs. Strength.
Preparing for ground conditions is foundational for successful equipment operation
Understanding and preparing for ground conditions is not just a safety procedure, it's a foundational aspect of successful equipment operation. Contractors and equipment operators alike must ensure that the ground can sustain the forces exerted by heavy machinery. Initiating clear communication with the controlling entity about ground-bearing pressures and set-up locations is imperative.
Visual site inspections by operators act as a final, crucial checkpoint to confirm site conditions align with reported data, ensuring a secure operational environment. With the availability of resources like DICA's Ground Bearing Capacity Chart, determining the appropriate supporting materials such as outrigger pads becomes a precise, calculated decision – not guesswork. Adhering to these practices will not only uphold safety standards but also enhance the efficiency and reliability of project operations.
*Canadians should refer to OHS Regulations, CSA Standards for Crane Safety, and provincial and territorial legislation.
Kris Koberg is the CEO of DICA.