Samsara fleet management solution saves Sterling Crane millions
Plug-and-play software suite includes driver safety, telematics, and digital maintenance tracking tools
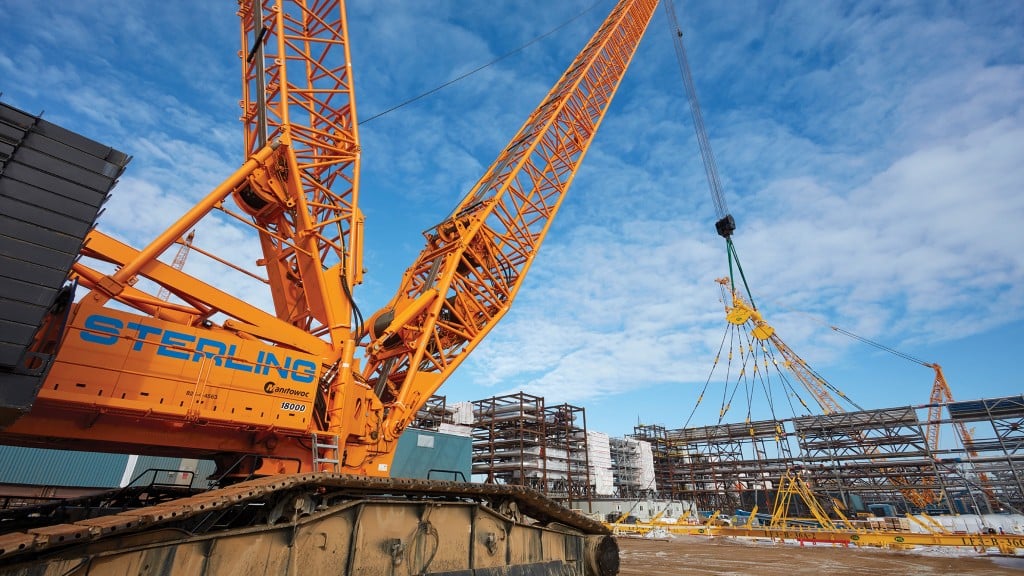
In the roughly one year since Sterling Crane integrated Samsara into its systems, the company has saved an estimated $2.5 million in major maintenance costs. Improved driver productivity and compliance adds up to $1.2 million, while more than 10,000 hours of technician time saved adds up to around $500,000.
Marco Goodridge is a busy man. As regional maintenance manager with Sterling Crane Canada, he and his team are responsible for around 900 pieces of equipment in Canada, and he needs to make sure that each of those pieces of equipment is being used correctly, is properly maintained, and is ready for work.
That's a daunting task, to be sure. For the 16-year veteran with Sterling Crane, finding the right tools for managing that fleet has meant some trial and error. Today, taking advantage of technology solutions from Samsara, Goodridge and Sterling Crane have a fleet solution that works for everyone, from the operators to head office. That effort hasn't gone unnoticed, as Samsara has named Sterling Crane its 2024 Connected Operations Award Winner for "Excellence in Systems Efficiency."
Massive fleet requires robust management solution
Sterling Crane is part of Marmon Crane Services and has 15 branch offices across Canada. It has been providing heavy lift services to Canadian businesses since 1954, and its fleet of cranes has grown steadily. Today, it is a broad, mixed-manufacturer fleet.
"We have various makes and models of equipment — we have cranes manufactured in Japan, Germany, the U.S., all over the place. Our technicians need to be well-versed on troubleshooting this equipment, and any technology we use needs to be compatible with all our programs," describes Goodridge. "They're all cranes, but they're all built a little differently."
With that broad scope of equipment, it made sense to explore technology options for fleet management. Sterling started on that path around 2016 with several goals: tracking equipment, understanding utilization, and better capture of maintenance information.
"In the past we would rely on our operators to scratch down the engine hours on their timecards, and those paper timecards would go to the administrators who would update our preventive maintenance program. But the administrators were super busy with invoices, payroll, all that good stuff, and updating our hour meters was sometimes low priority," Goodridge explains. "Our technicians had no idea when we needed to service our equipment."
First attempts with GPS technology showed some promise, but issues quickly arose. An initial deployment worked in some equipment, but in others caused technical issues — in cranes especially.
"Did they plug into our rigging and supervisor trucks? Absolutely, no problem. When it came to a [mobile crane], well — you plug it in, and . . . the system would fail. We'd be stranded on the side of the road scratching our heads," he recalls. "As soon as we unplugged it, the crane would be happy."
Technology failures eventually turned into one more thing on service technicians' plates, and that, among other shortcomings, sent Sterling Crane looking for a different solution that would work more smoothly with its fleet.
Goodridge was drawn to Samsara for the platform's broad suite of solutions that encompass key areas like driver safety, telematics, and digital maintenance tracking. Plus, he adds, it was a plug-and-play solution that worked with all of Sterling Crane's equipment.
Sterling Crane gets unionized labour's buy-in for driving data capture
Since implementing Samsara on its fleet, Sterling Crane has introduced a number of initiatives to take advantage of the system's range of capabilities, with the goal of improving efficiency across the board.
One deployment that has paid dividends thus far focuses on capture and analysis of driving data from Sterling's fleet of on-road vehicles. Dual-view cameras and sensors on vehicles detect specific incidents, such as hard braking, and capture video both in the cab and in front of the vehicle, which can then be reviewed.
Sterling's unions at first had some concerns surrounding privacy and constant monitoring of members when the cameras were first discussed, and negotiations were required prior to launch.
"It has taken a lot of education on our part. We've communicated and have had multiple meetings with our unions in every province to discuss," Goodridge describes. "We were a little hesitant at first to roll it out, but it's been a game changer for us."
Goodridge shared a look at the back end of the program with me to demonstrate the capabilities of the dual-view camera capturing inside and outside images. Video is captured when the system is triggered by a specific occurrence such as a hard braking. In some examples, the drivers are simply caught unaware. In others, they are either speeding or braking too abruptly.
For Sterling, it was all a reminder that the company needed to know more about its drivers and their habits — and a way to improve their results. A rewards system has created good-natured competition to determine the safest driver, with small gifts handed out each month to those in top spot. Buy-in has risen among drivers, Goodridge says, bringing safety and efficiency along as well.
Digitization significantly boosts proactive maintenance
Another new initiative is digitizing Sterling Crane's maintenance processing. Previously, technicians would have paper forms to fill out during inspections, indicating necessary maintenance to be performed. Those forms, Goodridge says, would then be scanned and emailed, sent through the regular mail — or not submitted at all.
"I could go to the branch for a visit and they'd have a pile of these [forms] sitting on a bench or in the office," Goodridge describes.
Now, technicians and operators are receiving tablets and digital maintenance forms that they can fill out and transmit directly through Samsara. When a technician looks over a machine in Ontario and finds an issue, they can take photos, make notes, then send the form immediately to Goodridge in Edmonton, and maintenance can be scheduled and completed much faster.
"Our goal for Marmon Crane Services is to have 80 percent planned maintenance and 20 percent unplanned," he says. "We don't want to react to something on the side of the road. We are now fortunate to be able to keep our eyes on the equipment and get accurate hours in."
Samsara saves Sterling Crane millions in maintenance costs
Overall, the results of adopting Samsara on the Sterling Crane fleet have been eye-opening for Goodridge and the company as a whole. A few hours a week per driver, technician, and operator add up quickly to thousands of yearly hours that can be used for more important work.
Financially, in the roughly one year since Sterling Crane integrated Samsara into its systems, the company has saved an estimated $2.5 million in major maintenance costs. Improved driver productivity and compliance adds up to $1.2 million, while more than 10,000 hours of technician time saved adds up to around $500,000.
Those results are central to why Samsara has named Sterling Crane one of its 2024 Connected Operations Award winners, who use data-driven insights to work safer, more efficiently, and more sustainably.
"It's incredible to see the tangible impact our technology has had on Sterling Crane, which has been serving Canadian customers for 70 years. At Samsara, we're always looking for new ways to help our customers take data from every aspect of their operations — whether it's driver safety, equipment monitoring, or employee workflows — and leverage it to solve complex problems," describes Charlie Cubeta, head of growth, Canada with Samsara. "Sterling Crane is a perfect example of this in action, having achieved such significant gains in efficiency and compliance less than a year into deployment."