Liebherr debuts flagship mining dozer at MINExpo 2024
The world's biggest hydrostatic drive dozer features operator assistance technology and remote-control compatibility
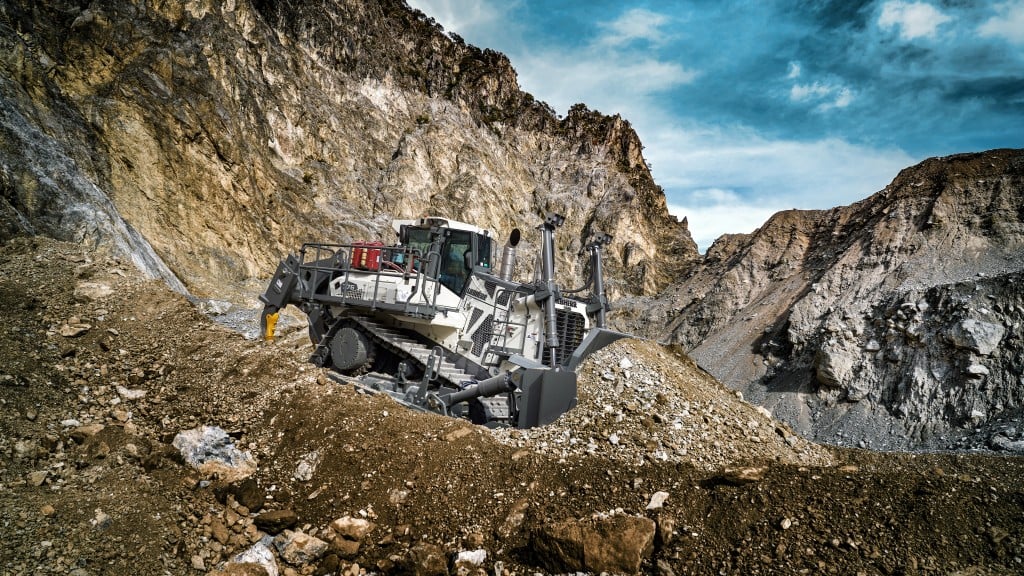
Debuted at MINExpo, Liebherr's flagship PR 776 mining dozer has been updated for the Generation 8 product line. Liebherr is currently the only OEM offering hydrostatic drive in this dozer class, and the PR 776 G8 is Liebherr's biggest dozer and the world's largest dozer with hydrostatic drive. Liebherr has introduced Operator Assistance Systems to its largest mining dozers, and the PR 776 G8 is compatible with Liebherr Remote Control (LiReCon).
The Liebherr diesel engine with the standard ECO mode allows operators to choose between high performance and maximum efficiency at any time. Fuel burn is an average of 38 litres per hour, and the availability of new assistance systems for these machines increases operator efficiency and ease of use.
Liebherr now includes Operator Assistance Systems on mining dozers
The PR 776 G8 crawler dozer integrates Operator Assistance Systems (OAS) previously available only on smaller dozer models. The new machine offers two levels of assistance systems: "Free Grade" for active blade stabilization during fine grading, and "Definition Grade" for automatic blade positioning when creating 2D grades. With the "Auto Blade Pitch" assistance system, the operator can save and call up three blade positions at the touch of a button: the right material penetration, optimum material transport, and rapid blade clearing at the end of the push path. The assistance systems of the PR 776 G8 are designed to not only increase productivity and efficiency, but also enhance operator comfort.
Liebherr dozer components are produced in-house for added reliability
For decades, Liebherr diesel engines have been used in various applications in construction equipment worldwide. Developed for the harshest operating conditions, their design and technology is built to ensure maximum operational reliability and longevity. The Liebherr hydrostatic drive system eliminates high-wear components such as gearboxes, steering clutches, or service brakes. Instead, hydraulic pumps and motors operate virtually wear-free, offering operational dependability. Liebherr offers numerous factory-fitted, field-tested adaptations for its dozers to accommodate various environmental temperatures, from desert operations to extremely cold conditions.
Generation 8 dozer designed for easy maintenance
Ease of service accessibility and extended maintenance intervals are key features of the new machine. Centralized maintenance points, wide-opening access flaps and engine compartment doors, a standard tiltable operator's cab, and an optional swing-out fan for cleaning facilitate quick maintenance access and straightforward servicing. The new PR 776 G8 has particularly long change intervals for operating fluids, such as hydraulic or engine oil. When using Liebherr Plus oils, these intervals can extend up to 8,000 operating hours, depending on the application and with regular checks.
Liebherr Remote Control system for dozers
When in a hostile work environment, for operators or machines, Liebherr Remote Control (LiReCon) aims to enhance safety, comfort, and productivity. The system is suitable for all dozer applications. It consists of the Liebherr remote control teleoperation stand; a state-of-the-art operator workspace including all required controls; and on-board dozer installations such as cameras for all different angles and views, microphones for recording machine sounds, and a radio link receiver and transmitter.
LiReCon allows fast shift changes between operators and consequently reduces idle and downtime. As the operator is no longer tied to the machine, it also enables customers to reach new extraction areas in hazardous zones, extending the range of applications.
Company info
1015 Sutton Drive
Burlington, ON
CA, L7L 5Z8
Website:
liebherr.com/en/can/about-liebherr/liebherr-worldwide/canada/liebherr-in-canada.html