Heidelberg Materials' Edmonton cement plant diverts over 100 kilotons of waste from landfills annually
Innovations include the replacement of up to 50 percent of fossil fuels with low-carbon alternative fuels
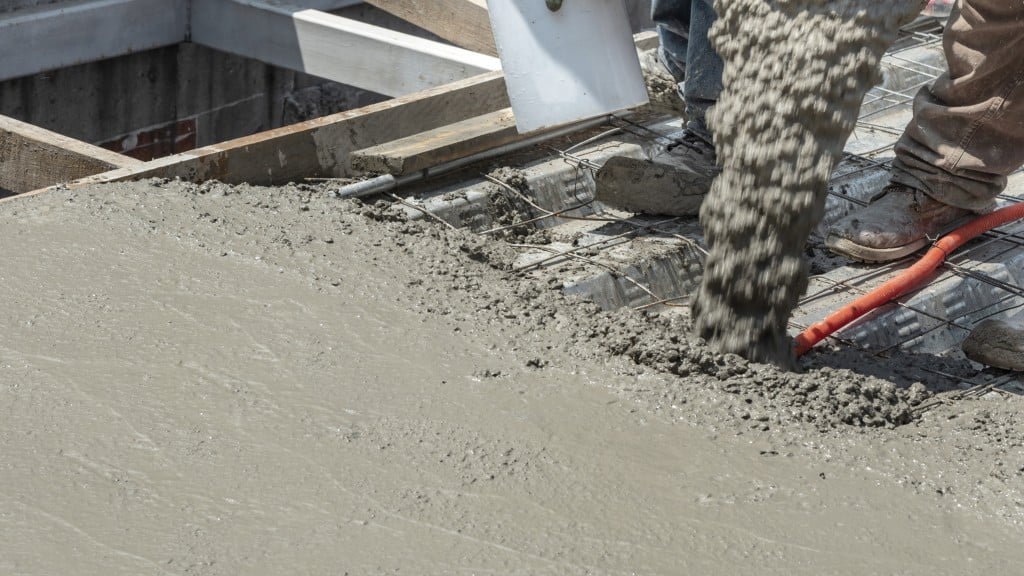
Heidelberg Materials North America has made significant environmental advancements at its Edmonton cement plant, marking substantial progress towards more sustainable manufacturing and waste management.
"At Heidelberg Materials, we are not just producing cement, we are crafting a sustainable future," said Joerg Nixdorf, vice president of Cement Operations for the Northwest region of Heidelberg Materials North America. "The advancements at our Edmonton Cement Plant reflect our leadership in environmental responsibility and our commitment to lowering our carbon footprint through innovative and efficient utilization of low-carbon fuel sources."
With support from the Province of Alberta through the Industrial Energy Efficiency and Carbon Capture Utilization and Storage Program and with a $2.4 million investment from the Government of Alberta's Technology Innovation and Emissions Reduction fund through Emissions Reduction Alberta (ERA), the Edmonton cement plant has made a major investment in cutting-edge equipment and infrastructure, enabling the replacement of up to 50 percent of fossil fuels used in cement production with low carbon alternative fuels (ALCF). These are sourced from municipal, construction, and demolition waste materials, which would otherwise end up in landfills.
Their environmental benefits include:
- Significantly reduction greenhouse gas (GHG) emissions from combustion, as biomass in ALCF replaces carbon from fossil fuels.
- Lower GHG emissions from avoided landfill gas emissions.
- Enhanced land use by extending the lifespan of existing landfills.
- Elimination of persistent environmental wastes, such as plastics, from the ecosystem.
Local waste managers in the Edmonton region, including the City of Edmonton's sophisticated Refuse Derived Fuel plant, process only non-hazardous wastes into high-quality alternative fuels. These fuels are then used as a consistent feedstock for the Heidelberg Materials kiln system.
"Advancing technology solutions that will help keep valuable materials in the economy and out of landfills makes good environmental and economic sense," said Justin Riemer, CEO of ERA. "Our hope is that any positive results or lessons learned by Heidelberg Materials will encourage others in the cement industry to do the same, giving this investment a greater, far-reaching impact."
As part of the project, Heidelberg Materials has implemented rigorous material testing protocols and process combustion control systems at both the supplier and plant sites to ensure the highest quality and safety standards. The project is expected to divert approximately 100 kilotons per year of non-hazardous waste from landfills, contributing to the global cement sector's drive for carbon dioxide emissions reductions through energy recovery from waste.
"This is an Alberta success story, as industry works to reduce emissions while keeping Albertans working and our economy strong," said Rebecca Schulz, minister of environment and protected areas. "We're proud to help support this project, which makes this facility one of the most advanced cement plants in Canada."