Choose a lightweight truck body that maximizes payload without sacrificing wear life
Durability and productivity can go hand-in-hand
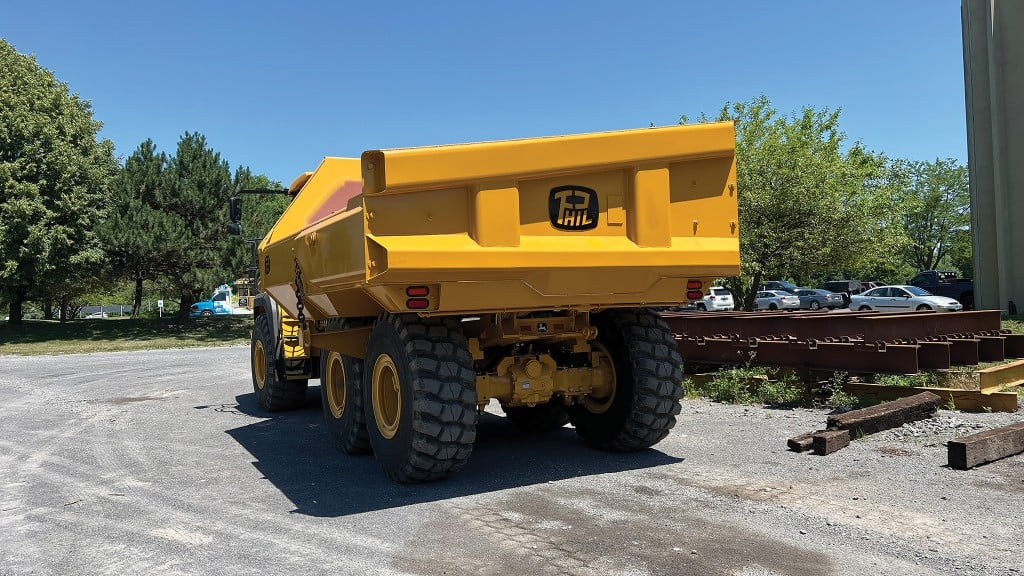
There are some things in life that make more sense, or simply become more useful, when paired together — milk and cookies, cars and heated seats, smartphones and an internet connection — the list goes on. Each of these items on their own provides some benefit. Add in the complimentary item to each of these though, and their benefit is elevated even more.
A similar anecdote could be applied in the aggregates industry when it comes to reducing weight and articulated truck bodies. Custom truck bodies are a significant investment and to truly realize the full utility of one — whether lightweight or standard — there are many factors producers must consider.
Custom vs. off-the-shelf truck bodies
The first consideration when looking at lightweight bodies is whether a custom solution to maximize productivity or an off-the-shelf solution is the right fit. For some operations, an off-the-shelf truck body does the job. For producers that want to truly optimize their operation, boost profits, and meet the growing industry pressure amidst the infrastructure boom, custom aggregates bodies offer what standard OEM bodies and other off-the-shelf bodies just can't.
When deciding on a custom body, look for a manufacturer that focuses on increased stability and operator safety in the design of custom haul truck equipment. Custom bodies should be constructed with a low centre of gravity to ensure the best weight distribution and minimize vibration to the driver as well as impact to the truck overall. Customizing individual truck bodies to the operation's specifications increases loading safety and greatly reduces the potential for loading damage by ensuring the truck body dimensions are correctly paired with the loading tool.
Another consideration is maintenance, and to truly maximize productivity custom truck bodies should address this concern. Some manufacturers add four free-floating lifting eyes into the body rather than the sides, enabling fast and easy removal or installation of a body for maintenance from a lower overall height without needing to go outside and use a portable crane.
Maximize payload with lightweight bodies
One of the key goals of a custom truck body is to maximize the amount of material an operation can haul with each pass. With a heavier payload and the weight of the standard body, maximum gross weight is reached very quickly in aggregate operations, limiting the amount of material hauled in each load. This creates a dilemma: add more trucks to the haul fleet or utilize the existing fleet more efficiently.
Previously, manufacturers used a thinner steel to reduce the body weight, which directly translated to increased payload capacity. However, the lighter-weight steel brought with it a shorter lifespan, often leading to the term "throwaway" body. In other words, producers had to choose between increased capacity or durability. And for some producers, the sacrifice in wear life of the body was worth it for the ability to haul extra material. Eventually, the need to change out the body after just a few years would frustrate fleet managers, and they would return to purchasing the heavier bodies that offered longer life and less maintenance.
The best of both worlds
But what if producers didn't have to choose between capacity and durability? It's a question that drove some manufacturers to research, engineer and manufacture options that offer the full benefit of maximized capacity in the form of a lightweight body that lasts more than three years. Producers can distinguish these more durable options from the "throwaway" lightweight truck bodies by looking at the quality of the steel. Some of the most durable options on the market are manufactured with Hardox 500 Tuf steel, which increases abrasion resistance by three times compared to 450 Brinell steel.
These lightweight bodies offer increased wear life while adding 10 to 20 percent to payload capacity. In terms of wear life, bodies engineered with 500 Tuf steel offer up to 30 to 40 percent more life than traditional lightweight bodies, creating an ideal solution that maximizes capacity without the extreme sacrifice in durability.
Choose to maximize the payload and lifespan
Quarry managers should not have to choose between maximizing haul loads and getting the best possible life out of their truck bodies. In addition to payload and wear life, producers should consider partnering with a manufacturer that looks at the big picture, including how the truck body fits into their operation, while maximizing operator safety.
If you give an aggregates producer additional payload capacity in the form of a lightweight truck body, they'll probably want some durability to go with it. And that only makes sense.
Josh Swank is chief growth officer at Philippi-Hagenbuch.