Is VR the future of workforce training?
ForgeFX delivers VR innovation for hands-on skill development
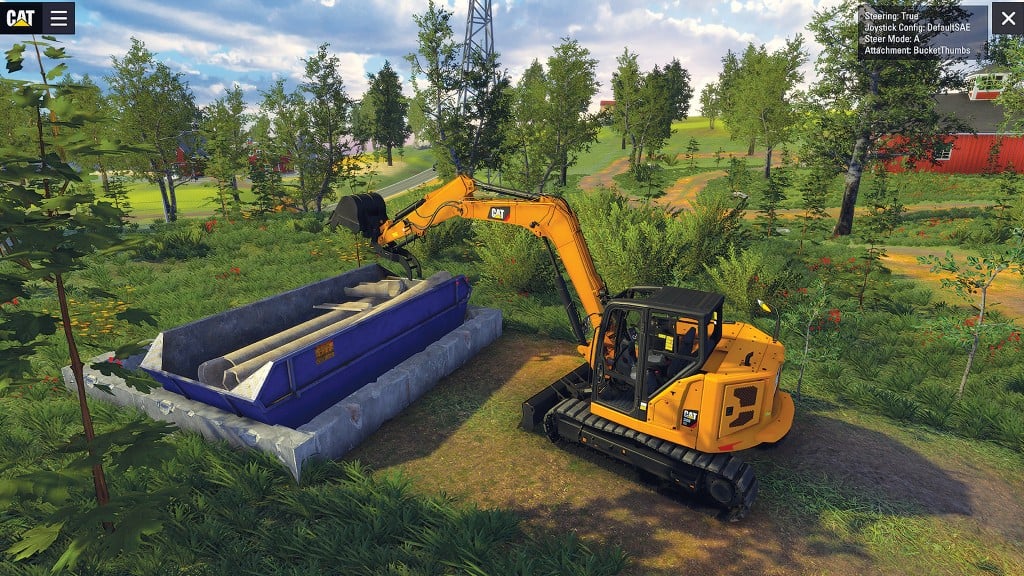
As the demand for skilled labour surges, industries struggle to fill critical roles, leading to delays, inefficiencies, and rising costs. With experienced workers retiring, fewer young professionals entering trades, and the growing complexity of job site demands, companies are scrambling to find new ways to build and sustain a capable workforce. Traditional training methods, lengthy apprenticeships, expensive on-site instruction, and outdated classroom material make it a struggle to keep up with the speed and efficiency required in modern construction and heavy equipment operations.
Imagine stepping onto a high-stakes job site before ever setting foot on the ground — mastering complex machinery, navigating hazardous environments, and making split-second decisions — all without the risks encountered on the worksite. Virtual reality (VR) training is an immersive, scalable, and cost-effective solution that can outfit businesses for more functional workforce development. VR is transforming the way industries train and develop their workforce.
From construction to heavy equipment operations, VR-based training enhances safety, efficiency, and engagement while reducing costs and helping employers overcome these workforce challenges by equipping trainees with the hands-on experience they need — before they ever set foot on the jobsite. ForgeFX Simulations, a San Francisco-based software company, is developing advanced VR training solutions for a broad base of industries.
The evolution of ForgeFX Simulations
Founded over two decades ago, in 2002, ForgeFX Simulations was an early player in developing high-quality simulation software for training purposes. As it evolved and refined its training systems, the company has collaborated with major industry players like Somero Enterprises and the US Department of Defense to create immersive training programs that replicate real-world operations in a virtual environment.
"Heavy equipment is one of the biggest users of VR training simulators," says Greg Meyers, founder and CEO of ForgeFX. In the last five years, ForgeFX has worked with organizations like Caterpillar to develop operation and maintenance training simulators and with Komatsu to develop systems that allow operators to train on underground loaders before the physical machines are even built.
Virtually transforming workforce development
While industries struggle to put skilled and capable boots on the ground, VR technology continues to evolve rapidly with solutions that streamline on-boarding, accelerate learning, improve retention, and reduce on-the-job risks. ForgeFX is optimizing training by developing realistic, accurate, and interactive learning environments.
Technology makes VR more accessible
Rapid advancements in VR hardware and software make the technology more accessible and appealing to a broader audience. Addressing previous limitations in user experience, these evolutions in VR technology create a user experience that is more intuitive, responsive, and immersive than ever before. Higher-resolution displays reduce motion sickness, wireless headsets are more affordable and eliminate cumbersome tethering, and improved tactile feedback enhances realism by replicating real-world touch and movement.
Artificial intelligence-driven interactions and adaptive learning systems provide personalized guidance, ensuring a seamless and engaging training experience for users of all skill levels. Newer generations of VR accommodate the integration of AI-powered virtual instructors allowing trainees to receive immediate feedback, boosting uptake efficiency and learning outcomes.
From theory to hands-on experience
VR-based training bridges the gap between traditional theoretical learning and hands-on experience. Instead of relying solely on textbooks, videos, or static presentations, trainees interact with realistic virtual equipment, gaining reflexive recall and operational skills in a risk-free setting.
ForgeFX has developed training solutions that allow operators to practice on heavy equipment such as excavators, drills, laser screeds, and aerial lifts in a virtual environment. These simulations use real-world controls and physics-based feedback to ensure that trainees experience the same challenges they would encounter on an actual job site.
The virtual training environment eliminates many obstacles to upskilling staff to be ready to go as soon as a job begins. Meyers explains that in many cases, operators can start training months before equipment arrives on-site. When the machine is ready, they're already proficient in operating it.
The ability to interact with virtual environments in real time enhances the learning process. ForgeFX integrates features such as hand tracking and stereoscopic vision, allowing users to develop critical spatial awareness and coordination.
Kristen Cox, business operations manager at ForgeFX, adds, "VR is particularly effective in industries where traditional training is costly, dangerous, or simply impractical. By the time workers transition to real-world machinery, they have already built the necessary muscle memory and confidence to operate effectively."
This technology is proving especially useful in scenarios where repetitive practice is required. Unlike conventional training, where access to machinery may be limited due to cost and availability, VR enables unlimited, consequence-free repetitions. "It really gives the user a sense of presence and agency within the [VR] environment, suspending disbelief so that they can really start to do things and make mistakes in the simulator, hopefully leading to the knowledge that makes them less likely to commit those same mistakes in the real world," Meyers says. "That's where the real value comes in — lowering risks and making sure trainees are fully prepared before they ever touch real equipment."
Enhanced learning retention and engagement
One of the biggest advantages of VR training is its ability to improve knowledge retention. A study completed by the National Training Laboratory, an American institute studying behavioural science, shows that VR-based training can improve knowledge retention by up to 75 percent, compared to 5 percent with traditional lecture-based training, reinforcing critical safety protocols before workers enter dangerous environments.
"This not only speeds up the training process but also reduces material waste and operational downtime," says Cox.
VR training reduces workplace injuries
Ensuring worker safety in high-risk industries like construction and heavy equipment operations is a constant concern that demands innovative solutions. VR allows trainees to experience hazardous scenarios without real-world risks, teaching them how to respond effectively in emergencies.
"We can simulate safety risks that are difficult to replicate in traditional training environments," Meyers says. "For example, with our horizontal directional drill simulator, we take the trainee underground, allowing them to see gas and water lines they must avoid hitting. This is something you simply can't do in real life."
According to a U.S. non-profit, the National Safety Council, mining, transportation and warehousing (materials handling), and construction are three of the top four most dangerous industries measured by reported workplace deaths. U.S. federal occupational health and safety agency, OSHA, reports that nearly 20 percent of worker fatalities in the U.S. occur in the construction industry, with falls, struck-by incidents, electrocutions, and caught-in/between accidents making up the "Fatal Four" causes of death. The use of VR training can significantly reduce these risks by allowing workers to practice in simulated environments where they can learn from mistakes without the risk of injury or loss of life.
Beyond accident prevention, VR simulations also prepare workers for emergency response scenarios, such as handling equipment malfunctions, hazardous material spills, or fire outbreaks. By practicing these procedures repeatedly in a controlled environment, workers gain the confidence and conditioned response needed to react quickly and correctly when faced with real-world hazards.
The cost of falling behind
While the initial investment in VR training might seem substantial, the long-term financial benefits are undeniable. From reduced material waste to lower travel costs, companies adopting VR training will see significant returns on investment.
One of the most immediate financial benefits of VR training is the reduction in material costs. Traditional hands-on training often requires expensive resources such as fuel, concrete, and specialized machinery which is subject to wear and tear. VR eliminates the need for excessive material consumption, enabling trainees to practice skills repeatedly without incurring high costs.
The U.S. Air Force is one of the largest end users of ForgeFX training simulators (distributed by Global Ground Support). "What the Air Force found was that they reduced the amount of the glycol deicing fluid that they sprayed by so much that they. . . estimated they saved half a million dollars in just one year by using virtual glycol instead of real glycol," says Meyers.
Companies will also realize substantial savings in travel and logistical expenses. Traditional training often requires trainers to meet employees at remote locations or for employees to travel to dedicated training facilities, leading to added costs for transportation, accommodation, and lost productivity. VR training allows trainees to access high-quality instruction from anywhere, eliminating the need for costly site visits and reducing downtime.
Beyond direct cost savings, VR training minimizes hidden financial risks. Workplace accidents and equipment damage caused by inexperienced workers can be extremely costly in terms of repairs, legal liabilities, and increased insurance premiums. By training workers in a controlled virtual environment, companies can significantly reduce these risks, leading to fewer job site incidents and lower insurance claims.
Improved training efficiency means that employees can reach competency faster, reducing the amount of time needed for on-boarding. "Instead of spending weeks or months shadowing an experienced operator before getting hands-on with equipment, trainees can familiarize themselves with the machinery in VR beforehand," Cox explains. "This means they're productive sooner, and companies can accelerate their workforce development without compromising on safety or quality."
As VR technology continues to advance and become more accessible, the cost-benefit ratio is becoming even more compelling. With proven savings in materials, logistics, and risk reduction, VR training can be a crucial tool for businesses looking to develop a smarter, safer, and more cost-effective workforce.
VR made accessible for small and mid-sized companies
Traditionally, high-end VR training solutions were exclusive to large corporations. Typically, a custom-designed VR simulation system will run between a quarter of a million dollars up to $1.5 million or more and take, on average, nine months to develop.
Meyers notes that many of their Fortune 500 clients, including Vermeer, JLG, and Komatsu, sell the simulator tools they paid to develop to their own clients (smaller contractors and operators) through their dealer networks. This allows small and mid-size businesses to access top-tier training at a fraction of the original development cost.
For many small and mid-sized companies, the barriers to implementing VR training have historically been the high cost of development, lack of in-house expertise, and limited access to the necessary hardware. But the growing affordability of standalone VR headsets and cloud-based training platforms is breaking down these barriers. For some businesses, understanding the ROI can prove that integrating VR-based training may be more affordable and accessible than they imagined.
Overcoming barriers to VR adoption
Despite the benefits, some companies remain hesitant to integrate VR into their workforce development programs. Two of the most common concerns are resistance to technology among an aging workforce and misconceptions about VR's effectiveness.
"We always hear, ‘You need butts in seats and hands on sticks.' You need people really experiencing that real-world equipment," Meyers says. "I don't disagree. We get a lot of pushback from folks who think that that is the only way to do it. I think that it's our responsibility to educate customers that you're always going to need that real-world training, but there is so much of that early machine control familiarization that we can do virtually. And there are some things that we can do better."
To ease the transition, ForgeFX involves experienced employees in the development process, ensuring that training solutions align with real-world industry needs. And, as expected, newer generations entering the workforce are already accustomed to interactive, game-like learning experiences, making VR an intuitive training tool.
The Future of VR in Construction Training
As VR technology continues to evolve, there are endless opportunities to expand this knowledge to further refine training and to pave the way for advanced autonomous equipment operations.
AI-powered training and real-time feedback
Artificial intelligence (AI) is set to play a crucial role in the next evolution of VR training. By incorporating AI-driven subject matter experts, trainees will be able to ask questions and receive real-time feedback within the simulation.
"A trainee can ask, ‘How much weight can I lift with this machine at 60 PSI?' and the AI will provide an immediate, precise answer," Meyers explains. "This eliminates the need to pause training and consult a manual."
Augmented reality and digital twins
While VR is already revolutionizing workforce training, augmented reality (AR) is poised to expand these capabilities even further. ForgeFX is developing AR-based training solutions that overlay digital information onto real-world environments, creating "digital twins" of job sites.
"Imagine a foreman being able to see real-time data on equipment performance, fuel consumption, and efficiency just by looking at a digital twin of the site," says Meyers. "This will take workforce management and training to the next level."
The road to autonomous equipment
In the long term, VR and AR training will be an important component in the advancement of autonomous heavy equipment. By simulating operations virtually as an early step, companies can develop and refine autonomous machinery before real-world deployment.
Meyers explains that building an autonomous vehicle starts with creating a virtual version of the equipment which operates exactly like its real-world counterpart. This digital twin allows engineers to program, test, and refine autonomous functions in a simulated environment — without consuming fuel, causing wear and tear, or risking operator safety.
"All of the autonomous vehicles you've seen started as virtual models," he says. "We build a digital twin, let it operate just like the real machine, and then begin training that virtual version to function autonomously."
This approach significantly accelerates the development of self-operating heavy equipment while reducing the cost and risk associated with real-world testing. As industries push toward automation, VR and AR will play a crucial role in ensuring that autonomous systems are efficient, safe, and ready for deployment before they ever touch the job site.
A training revolution in progress
ForgeFX Simulations is committed to ensuring companies that embrace VR training will gain a competitive edge in workforce preparedness and efficiency.
"VR training isn't about replacing traditional methods," Cox concludes. "It's about enhancing them and ensuring workers enter the field with the skills and confidence they need to succeed."
As industries using heavy equipment continue to evolve, one thing is certain: the future of workforce training is virtual.