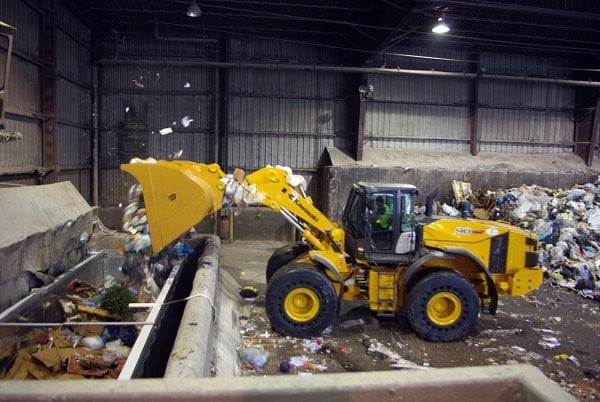
The third generation of the family that owns and operates J.P. Mascaro & Sons treats all 800 employees as if they are family. And the results are evident – the company has repeatedly been listed in Waste Age’s Top 100, which ranks firms based on annual revenue, even though they only operate in four states – West Virginia, New York, New Jersey, and in their home state, Pennsylvania.
Under the tutelage of Pat Mascaro, the President and CEO of J.P. Mascaro, the company is thriving. In fact, they recently signed the biggest contract in the company’s history – to operate two transfer stations for Morris County, NJ, one in Parsippany and one in Mt. Olive. The multi-million-dollar contract expanded their workforce by 70, and their machine fleet by 100 units.
The opportunity
The contract for the transfer stations is up for bid every five years, and when it came up for rebid in 2012, Waste Management held the contract. Waste Management had inherited the contract in 1999 when they bought the facility from the previous owners. Winning the contract would be a great opportunity for the J.P. Mascaro Company, and Pat Mascaro set out to win it.
He put together a team to look at the bid for the contract from every angle to make sure that if the company won the contract, it would be of great benefit to the company’s bottom line. Included in this arduous process was specifying and pricing all of the equipment that would need to be purchased to perform the work at the transfer station. Equipment Mascaro needed included 27 truck tractors, 68 trailers, as well as the replacement of five wheel loaders.
The wheel loader test
To ensure the equipment utilized at the facility would result in profits and permit compliance if J.P. Mascaro won the bid, the company set out to evaluate and test five different manufacturers’ wheel loaders. This was done in two steps. First, detailed research was undertaken by their Equipment Manager and Mascaro’s in-house engineering team. Second, live-application demos of five manufacturers’ wheel loaders were done at one of Mascaro’s yard-waste disposal sites.
The process took about two months to complete, including calls to every one of the end-user references each of the manufacturers provided. The team analyzed the weight class of wheel loader needed at the transfer facility based on the material that needed to be moved. When that was determined, the team got to work. They looked at the operation of the wheel loaders performing the constant stream of up/down and back-and-forth motion that using a loader in the transfer station necessitates.
The team could not rely on just the manufacturer or end user’s word on this one. They needed to make sure the loader’s hydraulics could handle the demands of the severe application and environment. They also investigated the durability of the tested loaders, as well as the availability of replacement parts – both items that, if not up to par, would seriously affect the transfer station’s profitability.
The wheel loaders at the transfer station are actively engaged in a dirty-by-nature work environment, so durability features like reinforced belly pans, hose protection, and a reversible fan to blow out the dust were necessary. The machines also need the ability to perform well in wild temperature fluctuations based on the season – sweltering heat in summer and bitter cold in the winter.
Additionally, due to the permit requirements of a clean and washed floor by 6:00 p.m., it was very important to the Mascaro group that the machines they put in place would be ready to work and allow them to meet that requirement with no downtime. If an issue were to arise, the company needed parts immediately available to perform the repair, because lost time would not only equal lost revenue, but it could equal fines as well.
With respect to profitability, fuel usage was also seriously studied by the Mascaro group. Given that their loaders actively work in the transfer facility with very little idle time, fuel costs were a huge consideration in evaluating the profitability of the operation. Information was gathered from the active demo site operators, and Mascaro’s in-house engineering team performed detailed analysis to find the highest performing fuel-efficient machines.
The reward
In the end, the Kawasaki 90Z7 wheel loaders met all of the facilities’ needs, and then some. And when J.P. Mascaro won the transfer station contract with their bid, the company purchased the Kawasaki wheel loaders from Steve White, VP Sales & Marketing at Elliott & Frantz in King of Prussia, Pennsylvania. Now, after being in use at Mascaro’s transfer facilities since January of 2013, their performance is even better than the testing originally indicated. The Kawasaki 90Z7’s Tier 4i Hino engine provides more fuel efficiency than anticipated, and they have experienced zero engine problems, according to the Parsippany facility manager, Mike Bosco. “The tailpipes of the loaders are sparkling clean after all this use,” Bosco said. “That proves they are burning clean.”
That Parsippany facility processes around 900 tons of waste per day on average, and loads an average of 36 large trailers per day. The Kawasaki 90Z7s are equipped with a 10-yard bucket with a rubber cutting edge, allowing operators the best visibility possible.
This also allows them to use the rubber edge to essentially squeegee the floor clean to comply with permit requirements at the end of each day. And because the Kawasaki loaders are equipped with excavator-like fine-precision hydraulics, the crew can accurately weigh the loads the loader dumps into the truck – making a return trip from the exit scales by the trailers a rare occurrence.
According to Bosco, Mascaro’s operators, one of which has more than 15 years running wheel loaders, are very pleased with the maneuverability, comfort, and durability of the Kawasaki 90Z7s. And Bosco is pleased, too. He has run and overseen the use of multiple kinds of heavy equipment, and is very impressed with the power and performance of the Kawasaki. “I have never seen hydraulic systems so precise,” he said.