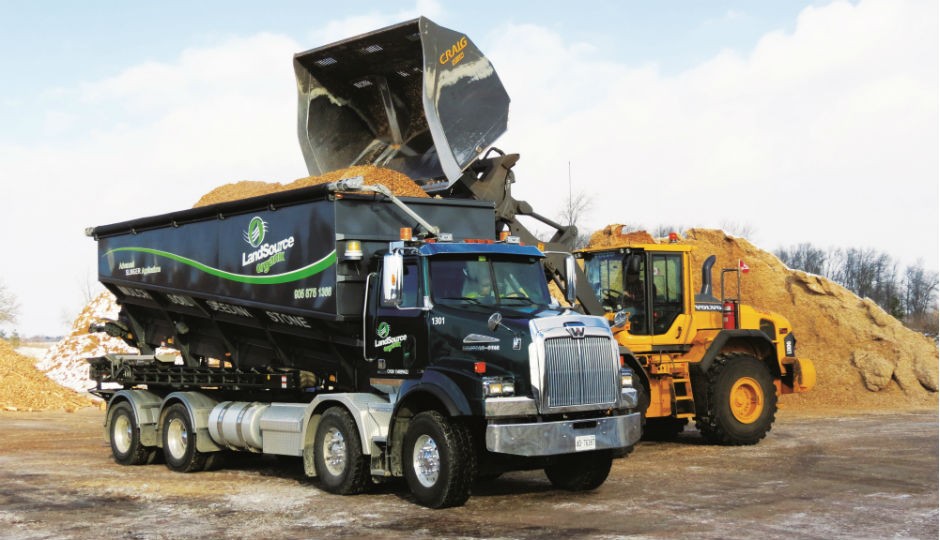
Andy Crocket is more than happy to show off the latest new idea in his equipment fleet: a 40-yard conveyor truck that he had custom built last year by the originator of the Stone Slinger system, W.K. Dahms. The high-speed Stone Slinger is typically used to accurately launch a stream of aggregates or soil into place from its hopper body at ranges of up to 100 feet. But Crocket had something else in mind when he decided to buy his specially designed model.
“The Stone Slinger costs about half as much as a blower truck,” said Crocket. “It made sense to me to use a slinger-type of truck as the delivery tool, so my blower trucks can continue operating without being interrupted to reload with material.”
Innovators collaborate on new conveyor truck features
When Crocket put his first blower trucks into service, he was breaking new ground in Ontario’s landscape business. Thirteen years later, Crocket’s Toronto-based business – Landsource Organix – is still innovating.
“When I started with my four trucks, I had the business to myself. Now there are a half-dozen businesses operating about 30 blower trucks in Ontario. I have to keep looking for new ways to be competitive and stay ahead of the pack.”
To make the Stone Slinger fit his particular needs, Crocket met with Scott Nelson of W.K. Dahms in St. Jacobs, Ontario. “Every other manufacturer we talked to had never seen this application; they were just focused on how far it or how fast it could sling. In our early discussions with Dahms, I threw out a few ideas. If they had been resistant or stuck with tunnel vision mentality, I knew it wouldn’t work. But they were quite open; I sensed that they even enjoyed it! They had fun building that truck because it was a little different.”
Nelson admits that he and his team appreciate the challenges brought to them by customers. “We are always developing new ways to improve the Stone Slinger. When customers bring us a wish list, as Andy did, it opens our eyes to new possibilities. We’re always interested in expanding the capabilities of our equipment in order to increase the productivity, profitability and reliability of our units.”
After Crocket presented his requirements to Nelson in the fall of 2012, he ordered a new Western Star 4900 SB chassis to become the platform for his Stone Slinger. The truck chassis, supplied by Near North Truck Centre in North Bay, Ontario, measures 109 inches from bumper to back of cab (BBC) and is powered by a 450-hp DD13 Detroit Diesel engine with a 10-speed Eaton Fuller transmission and 1,600 foot-pounds of torque. Weight distribution is 40,000 pounds on the front axles and 46,000 pounds on the rear axles.
About six weeks after the order was placed, Dahms delivered the custom unit. Its new features not only fit Crocket’s original application, it unexpectedly opened the door to new business opportunities and operating benefits for Landsource Organix.
“The first thing we needed was a higher, deeper box to carry 40 yards of material, to match the capacity of the blower trucks. Then we wanted to extend the discharge conveyor to reach right over the edge of the blower body. We don’t actually use much stone – we specialize in lighter materials like mulch, compost and wood fibre. By discharging the material directly into the blower truck, we minimize our clean-up times and put more material where we want it.”
Advanced controls for remote operation
The greatest challenge to the Dahms’ team, though, was to add a seeder system that injects seed into the material stream as it exits the truck, and then incorporate the seeder into the Stone Slinger’s remote control electronics.
“This is an excellent example of what you can do with CAN Bus technology,” Nelson says. “We introduced CAN Bus on the Stone Slinger to support remote control for the conveyor and drive systems. But its flexibility gives us a great platform for adding additional features to the system to suit customer requests.”
While most conveyor trucks are equipped with remote controls for the discharge operations, Stone Slinger now offers a remotely operated hydrostatic drive. The remote control can be used to move and reposition the truck wirelessly from outside the cab. Operators can maneuver the Stone Slinger to complete an entire project without once having to stop and get into the truck, disengage the PTO, move with the conventional drive, then set up again.
“It’s ideal for roadside seeding,” Crocket reports. “Where you’re close to the edge of a ditch or a slope and you want to seed, the operator can be walking along the side of the road and make a precise application, applying the soil and seeding it all in one smooth operation.”
“We weren’t sure if it was going to work when we took it up with Dahms, but it was worth the development effort to find out, and we’re pretty happy with it.” Scott Nelson and his team reworked the CAN Bus control system so Crocket’s operators could operate the seeder with the same remote control package. They also developed an extra wide feeder belt to increase the Stone Slinger’s discharge rate and further expand the range of products that can be handled.
While reducing the cost of his blower truck operations, Crocket has discovered that the capabilities of the new remote controlled Stone Slinger attracts new lines of business for Landsource Organix. The firm has emerged as one of the larger suppliers of engineered wood fibre in Ontario. Crocket’s crews have placed in excess of 3,000 yards of playground surfacing alone in the GTA in the past year.
“The Stone Slinger is a very cost effective tool for installing playground material,” Crocket explains, “and it offers a good price point.”
Apart from the difference in the cost of equipment, the Stone Slinger requires just a single operator, while the blower trucks typically travel with a crew of two. The Stone Slinger’s remote control makes it an ideal system for operating in close quarters around existing playground fixtures.
Crocket estimates that, with its playground projects and other specialized projects, the Stone Slinger spends 30 to 40 percent of its time this year doing work other than the reloading job he originally intended.
He says that getting the operator out of the truck cab is an important safety feature, too, even when it’s reloading blowers. The Stone Slinger operator has to move the slinger into a tight position to load the blower truck. With the remote control, he can do it from outside the truck, instead of with mirrors, and see the whole area from the best vantage point. Usually, the Stone Slinger truck is backed in to within 50 feet of the blower, then it’s moved with the remote from there. In its loading position, the Stone Slinger is close enough for its discharge to overhang the blower truck’s hopper body. “We have had no accidents, no bumps into the blower truck, through all of this year.”
After working with the new remote operated Stone Slinger throughout the past season, Crocket feels that his investment in customization has more than paid for itself. “The Stone Slinger attracts attention wherever it goes – even from teenagers walking by who have no interest at all in construction work. They see a truck working and hear it beeping with nobody in it! I tell customers I’m sending them the best Slinger truck in the world. When they see it they say, ‘now I know what you’re talking about!’ We spent a lot on that one option, but it has many safety and productivity benefits that add up.” “I think I’ve paid for it in this year, and I’ll get another 10 or 12 years out of it.”