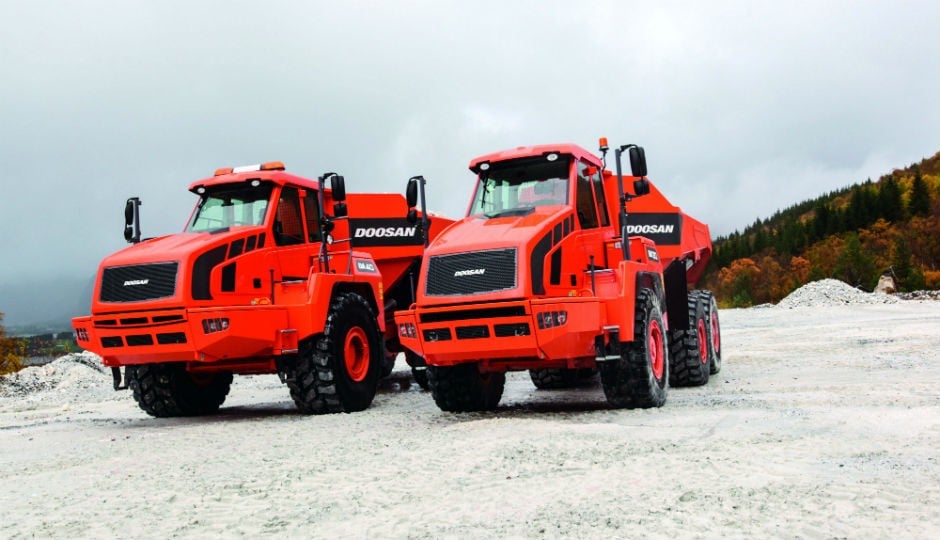
Doosan has introduced two new articulated dump trucks for the 28-and 40-metric-ton weight class, offering high performance, improved fuel efficiency, and increased reliability, serviceability and operator comfort. Doosan DA30-5 and DA40-5 ADTs have Tier 4 compliant diesel engines and feature improvements to the driveline, engine and cab for all-around operator ease of use.
The new 365-horsepower DA30-5 and 490-horsepower DA40-5 are powered by fuel-efficient Scania DC9 and DC13 diesel engines, respectively. The trucks have been configured with a high-pressure common-rail (HPCR) fuel delivery system as well as cooled exhaust gas recirculation (CEGR). Tier 4 compliant Doosan ADTs combine selective catalyst reduction (SCR) with a diesel oxidation catalyst (DOC) to reduce engine emission levels. Diesel exhaust fluid (DEF) is used with SCR technology and is stored in a DEF tank on the truck. The DOC transforms particulate matter (PM) emissions into harmless water and carbon dioxide. DEF is injected into the exhaust system to transform the nitrogen oxides (NOx) produced during combustion into water and nitrogen.
New to the DA30-5 and DA40-5 is a mass airflow sensor and exhaust brake, working in tandem to reduce emissions. The mass airflow sensor allows the electronic control unit to improve the management of airflow provided by the variable geometry turbocharger, and to optimize fuel delivery to the combustion chamber based on air intake volume and rpm. The exhaust brake helps to maintain consistent engine temperatures at lower engine speeds to improve operating efficiency. Consistent engine temperatures reduce harmful emission levels in the exhaust when the engine is running at lower rpms. Under normal operation, with high rpms, the exhaust brake is inactive.
Improved fuel efficiency
Following extensive hot and cold weather ADT testing with customers, which took place in 2013, the DA40-5 recorded an average of only 4.49 gallons (17 liters) an hour. The DA30-5 recorded an average of only 3.96 gallons (15 liters) per hour. Note: these results are operator and site specific.
Driveline improvements
Doosan strives to provide its ADT customers with the lowest and safest cost-per-ton transport rate. For example, the DA40-5 has a new bolt-on rear differential. The DA40-5 has improved gear ratios that provide reduced axle speed, improved component life, reduced vibration and lowered fuel consumption. It will replace the current one-piece rear axle. This design is a competitive advantage to further increase productivity and reliability, while reducing fuel consumption.
The new Doosan ADTs continue to feature a front-mounted turning ring, a sloping rear frame, tandem rear bogey and independent front suspension. The front-mounted turning ring helps keep all six wheels in permanent contact with the ground, even at a maximum turning angle. These ADTs are able to operate on very rough and soft terrain and are ideal for the mining and aggregate industry, commercial and residential site developments and infrastructure projects.
A sloping rear frame lowers the center of gravity for more equal weight distribution, and improved stability and safety when fully loaded. The sloping frame improves tractive effort, helps to minimize tire wear and lowers ground-bearing pressure. The independent front suspension improves operator comfort in rough terrain and assists in maintaining ground contact.
The tandem rear bogey delivers optimal traction with maximum ground contact in uneven terrain. Due to the tandem design, fewer points of power transfer mean less power loss and a more efficient driveline. All of these features to make sure the ADT maintains maximum ground contact and the best transfer of power to all wheels, allowing for reduced maintenance costs.
Simple service
A tilting cab gives service technicians excellent access to all of the truck’s major components. The cab can be tilted back in less than five minutes to expedite routine maintenance and repairs. New DA30-5 and DA40-5 trucks have only three wear parts on the entire rear frame, and they are greased by the automatic lubrication system. It is managed by the vehicle control unit and greases the various sections of the truck only when required. If the grease reservoir is empty, the transmission is limited to first or second gear only to prevent damage to the major components such as the turning ring and the tandem bogeys.