The heights of safety
Technology is playing a part in improving safe operation of cranes, both mobile and stationary
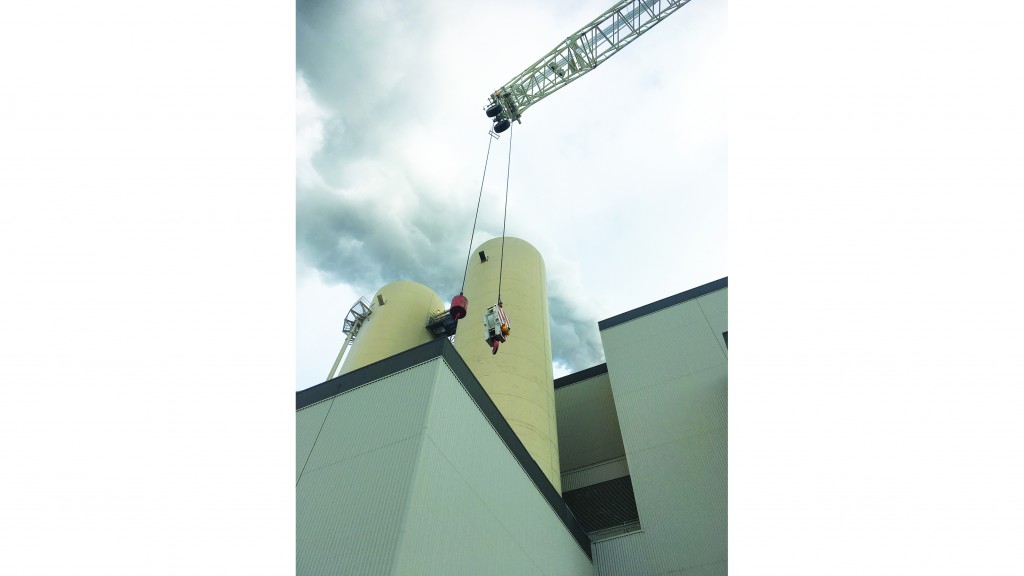
Cramped jobsites are becoming the norm for construction projects, especially in busy urban areas. The combination of multiple machines, workers, material and everything else is a challenge in itself, and the addition of lift equipment to the mix means that safety must be top of mind.
Mobile and tower cranes are essential for getting supplies around sites, and operators must be cognizant of the activity around them to ensure they and their fellow workers are as safe as possible. Along with good site planning and other approaches taken prior to the start of work, manufacturers are taking advantage of various types of technology to help with that goal.
"When they invented these cranes, they really didn't have the technology to be able to adapt them and enable the operator to work more safely - he just basically had to rely on someone else's eyes, and someone else's radio signal," said Chris Machut, chief technology officer with Netarus. "Now, there are things that range from anti-collision systems when you're working with multiple cranes to what we do, which is a magnetic deployable camera that allows the operator to attach his eyes, virtually speaking, right above the load so you can see how it's placed, how it's oriented, where it's going and who's around it."
Situational awareness improves safety
Crane safety comes from a number of directions, but starts with a good operating plan and operators that are focused and able to recognize problems quickly. Machut said that operators who can follow an OODA loop - Observe, Orient, Decide and Act - are a key part of safety, and technology that helps them in that goal is important.
"Having an operator that has really good situational awareness in his environment is really part of the whole plan," Machut said.
There are plenty of safety practices that come along with crane operation, starting from the site's lift plan and extending out to a range of checklists, knowledge of the loads to be picked, the positioning and so forth. Technology takes those practices a step further, Machut noted.
"What we push for is how you extend beyond the standard safety practices - not necessarily to replace them, but to actually augment and assist them," he said. "That goes into understanding and incorporating things like visual aid technologies into the lift plan and the processes that are critical to every operator."
The HoistCam camera system from Netarus was developed to help give operators an additional eye on the load, which is especially important when running a tower crane or lifting over an obstruction, for example. A remote camera is attached magnetically to the hoist. It can run for up to 24 hours, broadcasting video to a monitor in the crane's cab.
Camera adds extra eyes on operations
"Many tower cranes have 120-volt AC so we can plug into that, or in mobile equipment, 99 percent of them have a cigarette lighter plug in them so we have adapters for those as well," Machut said. "Setup is literally a couple of minutes. . . and the rapid deployable nature of the system makes it very easy to use."
Operators find having the camera gives them more control of the situation around their machine, and improves safety significantly.
Machut said that he has received calls from operators who report that they have experienced near misses on the job that, without the camera giving them a chance to take a second look at the situation, could have created serious incidents and potentially fatal consequences. "We're not talking about shutting down a crane for a day due to an accident, we're talking about not shutting a crane down because he spent two to three seconds verifying that everything was safe."
Mobile cranes have their own unique safety challenges to consider. With many contractors opting for mobile machines for their flexibility, the need to move through tight spaces and then set up the crane for lifting in close quarters with other equipment has driven manufacturers to develop a variety of technologies to assist.
Liebherr, for example, has paired its mobile cranes with the LICCON control computer, which monitors many aspects of crane operations, including safety. Lee Spalding, a sales representative with Liebherr, said that the company's systems are a way to back up the operator in difficult spaces.
"Liebherr is really on the forefront of that technology - for example, there's a new counterweight monitoring system on newer cranes; there are sensors in the hydraulic jacks that lift the counterweight, and when the operator has to confirm everything on the computer and puts in a value that's different than what the computer is telling him, he'll get a warning," Spalding explained. "In this case, the computer may say that he has 100 tons of lift and he's putting 80 tons in, so it will provide a warning and he can double-check."
Some of the company's cranes are equipped with VarioBase, a technology that allows the operator to set the outriggers at independent lengths, a feature that means the machine can fit into restricted jobsites where the outriggers might need to be different lengths. The system takes the outrigger positioning and calculates a load chart for the position, as opposed to having a paper load chart calculated ahead of time. From there, the operator is able to use a software package to plan lifts where necessary, either on a personal computer or within the LICCON system.
"If the crane operator is sitting in his crane and doesn't have a laptop with him, but someone comes up and asks him if he can do a lift, he can press a button on his LICCON system and it will switch into a virtual mode - he can plug in his parameters and do the lift virtually, with the joysticks and everything, as he sits in the crane," Spalding said.
Visibility when setting up a crane is important as well; operators are often stuck in the cab without a full field of vision around them while the setup process is ongoing, or must use control panels on either side of the crane to extend their outriggers and other equipment. Liebherr has taken advantage of Bluetooth technology to give the operator more opportunity to view the surroundings while setting up.
"When you get to a jobsite, you pull the Bluetooth device out of the dash, get out and you can start setting up with this device," Spalding said. "You can walk around the crane as you're setting up, looking for obstacles. . . once you have the outriggers and axles locked and the crane is ready to raise up, you press one button and the crane will auto level."
While the unit allows operators to do most of the machine setup and get ready to move, a new option also allows for the machine to be operated by remote control - one remote control unit can work with multiple cranes using the Bluetooth device from that machine, Spalding said.
"That operator could be standing on a roof while they're placing an air conditioning unit - everything that's on the LICCON system in the cab is displayed on the remote control unit," he said.
An operator can even drive the crane from point to point on the jobsite with the remote control - an added safety measure in crowded spaces, Spalding noted.