Bridging the gap between concrete batching and dispatch systems
Sensors and software from Coretex keep ready-mix fleets moving efficiently
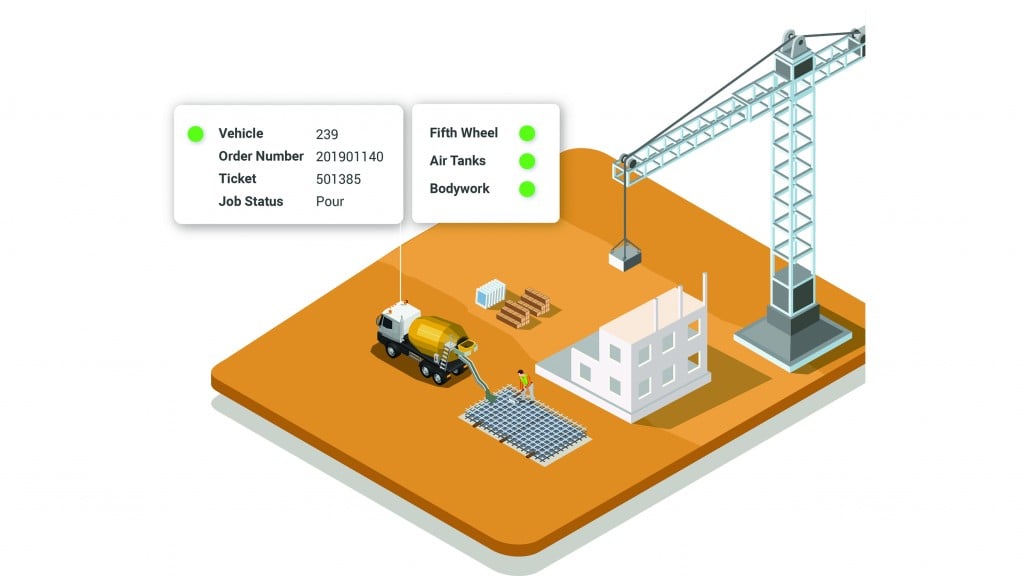
There are challenges in managing any large fleet, but when that fleet carries a potentially perishable cargo that must be precisely handled and delivered on time every time it adds to the complexity significantly.
Concrete needs to get to jobsites in good condition and on time. If there's a problem with a mixer truck - it gets lost, or breaks down, or simply just lags behind - then that's a problem for the material it carries. If there are too many trucks heading to a job at once, that's a problem too. Frankly, just about anything that doesn't involve arriving on time and placing that mix where it needs to be is a problem.
There's no way to completely ensure that every delivery will be perfect and precise, but mixer fleet managers do have options when it comes to tracking and planning for their trucks' movement and needs.
Coretex, which develops telematics for a variety of fleet operations, has targeted ready-mix fleets for optimization with a range of tools that can help managers and drivers keep on schedule and meet their delivery goals.
"They may have done the most incredible batching of the perfect mix, but one of the issues they have is when it leaves the batch plant and goes to the contractor's location, there's a mystery of what can potentially happen. That's where we've come in," said Dean Marris, executive vice president, construction materials with Coretex. "You can have an array of concerns with the vehicle from a fleet management point of view where you suddenly have an issue like overheating, you could have an issue where you have water being added in on the jobsite that's compromising the actual load. You could just be looking, from a utilization point of view, at too many trucks, or not enough, so there's a real balance in terms of dispatching and the batching staff getting that part right."
Currently, many fleets - especially smaller operations - use the traditional method of fleet management for concrete mixers: the good old paper ticket. The driver gets a ticket and instructions on where to deliver the load, and off they go. Larger fleets are starting to integrate their tickets with electronic dispatch systems, Marris said.
"The truck receives the tickets electronically, along with instructions so they're guided to the specific location," he said. "So, depending on the fleet size, there are different technologies out there."
Many ready-mix trucks are equipped with sensors that can connect to the dispatch system as well, providing status reports on the mix, the truck's operation, and other factors. All of that requires a lot of software that often doesn't meet in the middle.
"Typically you have batching software and then you have dispatching software - the company is talking to other companies that are connected in to that dispatch software, and there's nearly real-time communication back and forth."
Coretex, with its solutions including Coretex 360, can bridge the gaps between batching and dispatching software, and help give dispatchers the real-time decision-making opportunities that ensure their fleet is running as smoothly and efficiently as possible.
"Where we come in is, we provide the fleet management system that gives the visibility for dispatching people, and they can make real-time decisions with the information that's being sent back from the truck," Marris explained. "For example, a truck can be ticketed and loaded, and we can see water has been added, and that it's left the plant. We know when it's arrived at the jobsite. All of this is talking to the dispatch system, so that dispatching knows straight away that the nearest truck has arrived."
Waiting times at the jobsite can be cut down as well, something that saves money for both the fleet and the contractor, Marris noted. According to the U.S. National Concrete Association, every minute a truck is waiting to pour costs $1.75 - an expense that can easily be avoided.
"If the trucks have excess waiting time, that's something that we look really closely at," he noted. "The truck in front, the truck behind, the time intervals between trucks arriving at the site - these are all real-time decisions the dispatcher can make."
Coretex integrates with the dispatch system to ensure that the communications are handled, and adds a tablet that is installed in the truck to give drivers key information on deliveries and other details.
From there, the system is able to take data from things like drum rotation and other sensors on the truck; that information can then be broken down through an analytics solution, which owners can then make use of in maintenance and sales efforts.
Electronic logs and other regulated entries can also be done by the driver, with easy and low-maintenance equipment installed in the trucks. Driver Vehicle Inspection Reports (DVIR) are moving forward quickly in the ready-mix industry, Marris noted, providing owners an opportunity to improve their response time to problems.
"If you're in a situation where a chute isn't working properly, say, the driver can fill in the DVIR to say ‘hey, this needs to be looked at,' and the alert can go straight to the mechanic electronically - he then knows at the end of the day that he needs to get there and fix it so the vehicle is back on the road," he said. "That has been quite refreshing for our clients - they love the fact that they have integrated statusing, real-time information to the dispatchers, and the fleet management part all in the one solution."
In addition, the Coretex solution can integrate with a variety of other technologies, ranging from video capture to safety and more.
Implementation of Coretex solutions is easy, with the company providing rugged and reliable sensors and in-cab equipment for a monthly fee through its subscription-based service. Pricing is designed to make the service a good option for ready-mix fleets large and small.
"This technology provides real-time decision-making," Marris said. "This is why I think people are considering this type of technology onboard. . . this industry has been a little behind compared to other verticals, but I think they're listening."