Revolutionary cab is focus of Dressta dozer design
The new TD-16N dozer is the result of a seven-year design process focused on improving operator visibility and safety
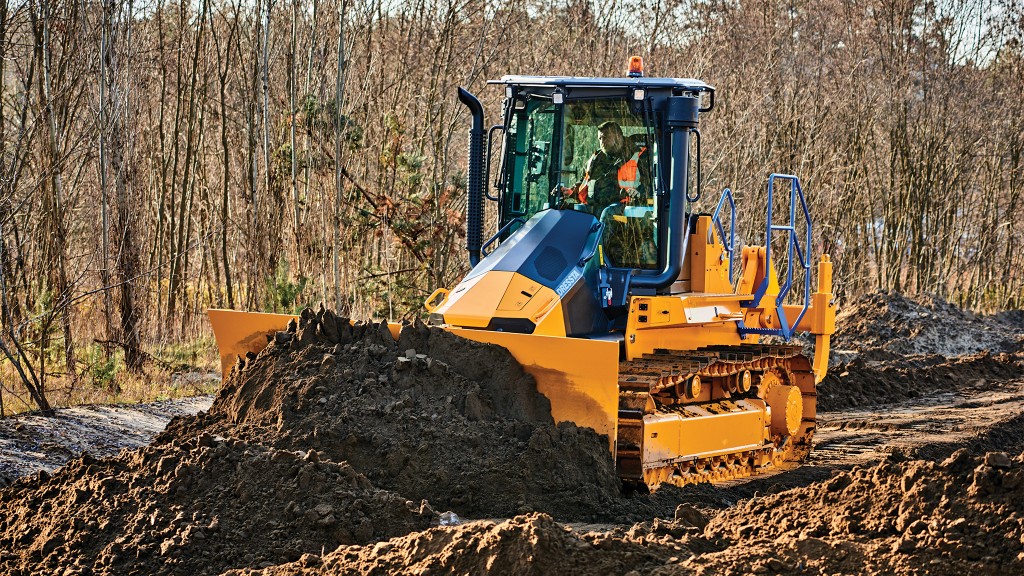
Construction equipment is often designed for power and strength, ensuring the machine can handle the rigours of its task on the jobsite – digging, pushing, lifting and so forth. At the centre of that machine, however, is the one key part that makes all of that happen: the operator.
With today's labour challenges driven by an aging workforce and other factors, manufacturers are giving contractors tools to help attract good equipment operators, and cab design has become an area that many companies have focused on. The more comfortable and safe a cab is, the more likely it is that operators will stick around to use that machine for its owner.
One feature that is often a challenge for designers is visibility. Construction equipment is hardly streamlined or aerodynamic; the bulk from counterweights, big engines and other aspects that make it possible for a machine to do its job are difficult to design around. At the same time, making it easier to see the area around the machine immediately improves safety for the operator and everyone on the ground.
Operator's needs are the design starting point
When track dozer specialist Dressta set out to design the newest machine in its range, the TD-16N, the cab was, in many ways, job one. The team behind this new dozer wanted to revolutionize the operator's ability to see the jobsite around them.
"In the past, and I'm including my 32 years in construction equipment, the cab enclosure had been little more than a means of keeping the operator dry in the rain and cool in the sun - it was basically a shelter," described Gary Major, director of industrial design with LiuGong Dressta. "As the operator interface has changed and safety requirements have rightly improved, the cab has become the most important aspect in designing any new product."
Older machine designs didn't take the operator's needs into consideration, noted Edward Wagner, LiuGong executive director of new technology.
"You don't have to look too far back in time to find heavy construction equipment was designed to optimize the machine for simplicity and low cost with little to no regard for the actual operator. Anyone who has spent a 12-hour day running a machine with an open cab, or no cab at all, can understand this – the old machine would literally beat up the operators," Wagner said. "Finally, owners began to realize there was a cost advantage to having the operator stay comfortable and productive throughout the day."
Even with that in mind, many machines are still designed based on the needs of the machine layout and without a lot of thought given to how that design affects the operator. "We flipped this with the design of the TD-16N, as we literally started with the operator and their needs, and built the machine around them," Wagner noted.
Dressta determined that it was time to consider updates to its dozer line, and approached the TD-16N as a starting point for that process, Wagner said. "The legacy machines needed enough updates that it actually was a simpler and faster route to make a clean sheet design for this large hydrostatic dozer." Major said the ground-up approach to the new machine meant the design team had a lot of freedom to meet their goals.
"The TD-16N is a ground-up new concept, propelled by one primary goal – to build a bulldozer with unrivalled levels of visibility, safety and comfort," he said. "This, of course, meant a total rethink of traditional dozer packaging and the cab was an intrinsic part of that focus – you need to take a holistic view of the machine, as opposed to looking at individual components."
Seven-year process
Design on the TD-16N started in 2013 and spent two years as a "black" project with just a few people privy to the process before the engineering team was brought on, Major said. The first steps focused on what Wagner described as a "pyramid of principles" that guided the team's approach. The operating needs of the machine – the blade and track size and orientation – were the base of the pyramid, but the centre was the customer, defined as the owner, operator and mechanic who will own and run the machine, Wagner said.
"We literally optimized the location of the operator with respect to the blade and tracks, and only then did we start the design of the rest of the dozer around those needs," he explained.
There was some pushback when the design process started, mostly thanks to fear of the unknown, Wagner noted. Some suggested that the team would be better off building a more traditional machine, but as the project advanced, those attitudes began to change.
"Once we had the basic layouts finished, many peoples' fears subsided. After our first prototype was built and people could see it really was going to work, the team gained momentum and confidence," Wagner said.
While innovation was the biggest driver of the process that led to the new machine, it was paralleled by LiuGong Dressta's overarching principles as well, Wagner noted.
"The tip of the pyramid is our own company needs, such as maneuverability. Consistent with our design philosophies, we proved yet again that a machine designed to be easy to service and repair is also quite easy to assemble in the factory."
Striking new dozer design
The result of this process is an entirely new dozer that provides what Dressta states is unparalleled visibility for the operator. The new cab design is striking in the size of the windows that wrap fully around the operator station; from the seat, the design of the machine body takes advantage of all that window space to allow the operator to see 309 degrees around the machine. Steep angles on the front of the machine and no obstacles elsewhere make the visibility excellent all around.
"In order to meet our aspiration for operator visibility, the DLO (daylight opening – a frequently used automotive term) ratio is much greater than any other cab on the market, something emphasized by our choice in using flat glass throughout," he said. "The decision to use a planar glass laminate was primarily for optical quality (for example, zero distortion) with ease of replacement second."
Flat glazing also helped enhance the overall aesthetic of the machine, he added.
All of that glass did bring some unique concerns to the table, however: added thermal loading.
"Addressing this task has been done in collaboration with industry-renowned HVAC specialists; plus, we have topped the cab with a roof moulding painted in light-reflecting silver, a surprisingly effective detail," Major said.
The TD-16N, introduced at CONEXPO 2020, has a strikingly unique design in a machine that can handle operator needs on the jobsite. It features an automatic dual-path hydrostatic drivetrain and standard six-way angle blade; compatible with 2D and 3D grade control systems, the machine generates 170 hp and has an operating weight of 19,090 kg or 42,090 pounds.
New access point concepts
Carrying on the desire for improved safety, the machine also features access points that mean the operator never has to climb onto the tracks to get in to the cab. Plus, all daily check and maintenance access points are reachable from ground level.
The results of the seven-year design project generated plenty of discussion at CONEXPO, Wagner noted.
"Some of the key customer concerns I heard were: ‘Finally, a dozer designed by someone who operates dozers,' ‘I can't believe how much I can see; this will make my work both faster and more precise;' ‘why didn't anyone do this before?'" he said.
Dressta chairman Howard Dale said the TD-16N will benefit in improved safety and productivity for owners. "The superior visibility of this machine will certainly help operators be more productive and do a better job in less time," he said. "We also know that this machine will make the worksite safer for everyone."
This article originally appeared in the May 2020 issue of Heavy Equipment Guide.