Top safety tips for working around crushing and screening equipment
There are many ways to potentially face harm around aggregates equipment, but a few simple safety tips can help improve job site safety
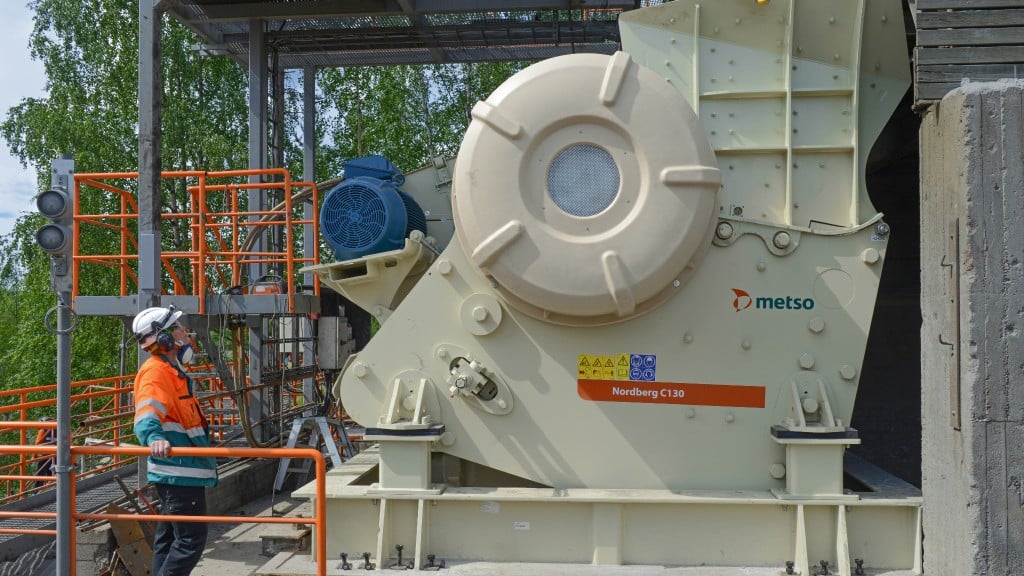
Working around crushing and screening equipment brings plenty of potential dangers. There are many ways that a careless employee could potentially face harm around aggregates equipment, but a few simple safety tips can help improve jobsite safety for crushing and screening operations.
Avoiding complacency
The biggest safety hazard in any quarry or recycling site is complacency; when employees have become too comfortable with their tasks and the equipment around them, according to Metso technical training instructor John Starck. Speaking during a recent webinar hosted by the company, Starck pointed out that of 14 fatalities that occurred in the U.S. related to crushing and screening work, eight were highly experienced workers.
"Often, it's the people who get complacent around machinery that are the ones that get the most injured. Ask yourself if you know people who are complacent around equipment, and ask yourself if you're one of those people," Starck said.
That complacency can be shown by the use of certain common phrases in the workplace, Starck said, such as "this is the way we've always done it," "we tried that already; it doesn't work," "it'll take forever if we do it that way," and "what do they know?" Those phrases should be removed from the equation, he advised.
Five key tips for reducing hazards on the crushing and screening jobsite:
Keep Mondays for planning: Monday has proven to be the most dangerous day of the week, with labour statistics showing it to be the day on which most workplace injuries occur, often within four hours of starting a shift. "With this stat in mind, the safest approach might be to use Monday as a planning day for an upcoming repair," Starck advised.
Use the observation process: Complacency can be driven by employees doing repetitive tasks, Starck said. "As a task becomes routine to an employee and the fear of getting hurt lessens or, worse yet, no longer exists, it's easier for your mind and body to wander," he noted.
One way to reduce that complacency is to introduce an observation process, where another person works alongside the employee and provides feedback. This can improve work habits for both employees such as properly wearing PPE, better lifting habits, and more. "The bottom line to fight complacency in the workplace is that you have to do something that actively gets people involved and thinking about the hazards involved in the task," Starck said.
Read safety plates, decals, and symbols: Every machine comes with these warnings, and employees need to keep them in mind near the machines. According to Starck, Danger indicates immediate hazards or unsafe practices that will result in severe personal harm or death, Warning indicates unsafe practices that could result in personal injury or death, and Caution marks hazards or unsafe practices that could result in minor personal injury or equipment damage.
Keep manuals available for everyone: Instruction manuals and parts books should be kept nearby on the jobsite for all employees to access, Starck said, since they are invaluable tools that contain key information for repairs and other activities.
Good housekeeping: Starck noted that slips, trips and falls make up the majority of workplace injuries, and suggested some ideas to reduce that potential danger, such as identifying safety hazards, using three points of contact on ladders, exercising caution climbing or descending staircases, using handrails, never jumping from equipment, and using fall protection.
"I know taking your time sometimes doesn't go well in our industry because we're always in a rush to get things done, but if you're in a dangerous position, please slow down and take your time," he advised.
Safety hazards near crushers
Every type of crusher operates a little differently, but they all have the potential to cause serious harm to anyone who doesn't take care in dealing with them, Starck said. Stored energy, whether rotating or pressurized, can cause serious harm if not guarded against.
"We should always be aware that these hazards exist - jaw and impact crushers have significant stored energy in rotating energy, while cones and jaws can have significant pressurized or stored energy," he said. "There is a lot of machine inertia - make sure that inertia is stabilized before you even start work on it. Crushers will continue to rotate slowly during their coast-down time, which creates a potential safety hazard - all personnel must stay clear of the crusher and rotating elements until the machine has come to a complete and final stop."
Jaw crusher safety
Jaw crushers can move unexpectedly if the machine flywheel counterweights aren't in the right position,Starck advised. When viewed from the feeder, looking in the direction of material flow into the crushing chamber, the left-hand flywheel counterweight needs to be in the 1 o'clock position, while the right-hand one needs to be at 11 o'clock - in this position, the eccentric lobe of the crusher will be facing down and the pitman will not move unexpectedly, he said. If the counterweights are not in this safe position, the flywheel must be fully secured before any work should begin.
Crushers may occasionally be jammed up by oversized or blocky feed; if this occurs, Starck said, both the crusher and feeder should be locked out and tagged out, and a hydraulic hammer should be used to clear the blockage. Employees should be equipped with fall protection in this process, Starck added. If the hammer doesn't work, a crane with a lifting strap or cable should be used. Never use steel bars, wedges or hooks to remove material while the crusher is running - this has proven fatal in the past.
Stalled jaw crushers may be jammed with tramp material that could potentially be ejected with fatal consequences, Starck said. A jammed crusher should be locked out and tagged out, then the crusher setting should be opened - this will usually release the pressure on the tramp and allow the crusher to be dug out. Remember to check the flywheel positions as noted above, he added.
Cone crusher safety
Stalled cone crushers may also be jammed with tramp; in many cases, these machines have some sort of hydraulic clearing system that should be engaged, and if that doesn't work the owner should have a written procedure in place for clearing the blockages.
Where cranes are being used to remove problem material or lift heavy components for maintenance, Starck said it's important to ensure the crane is only used within its rated capacity, that adequately sized and well maintained cables or straps are used, and other best practices be kept in mind.
"Another safety hazard is having too many people telling the crane operator what to do - there should be a dedicated signal man who is the only person allowed to give the operator signals, and the only person the crane operator listens to," he advised.
Other considerations
Starck pointed out several other areas in which staff must exercise caution while doing repairs or maintenance around crushing equipment, including electrical and hydraulic systems as well as repair and replacement of equipment guarding.
He said that Metso has a corporate focus on safety to ensure that its customers are as well protected as possible, and that they encourage others in the industry to do the same.
"Ask yourself every morning: is today going to be a safe day? Because your loved ones are relying on you to be safe, and come home."