Nailed it: rock drill gives contractor edge on large nail wall project
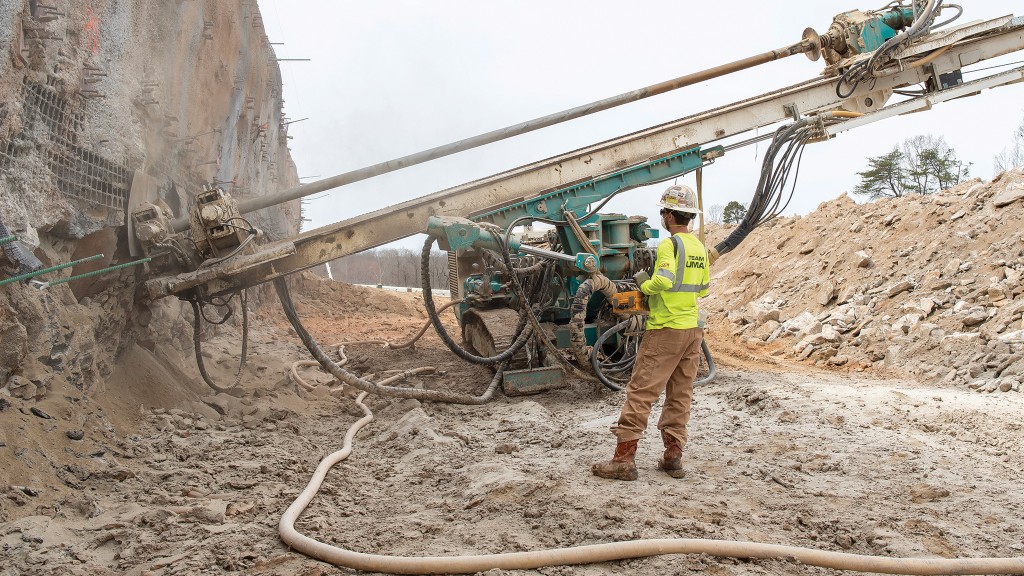
When a major interstate project required a large soil retaining wall to be constructed for stability and safety, UMA Geotechnical Construction went to work – designing and building 42,000 square feet of soil nail wall in the project. As a subcontractor to Flatiron Construction, which was building 1.5 miles of divided highway, UMA spent around two years on the project from design to completion in 2019.
"The soil nail walls were designed in-house by UMA," says President Brian DeSpain, adding that the company utilized licensed engineers on staff. "The state identified the locations and it was up to us to figure out how to design the most cost-effective system."
Unlike many such wall projects, though, Wall 4 was a bit more of a challenge thanks to its size and challenging conditions.
UMA's scope on Wall 4 was straightforward. The job was essentially to install soil nails and a temporary shotcrete facing to allow Flatiron to finish it off with a cast-in-place concrete wall. However, due to adverse geotechnical soil conditions, a simple install became increasingly more challenging. In a budget-saving triumph, UMA's proven history and competent personnel made light work of the challenges.
At just over 30 feet, the height of Wall 4 towers above anyone standing at its base. Once completed, it is 42,000 square feet and just over a quarter mile long. To provide context, 12,000 square feet is an average sized wall. Of the seven other walls UMA built on the Greensboro Western Loop, the average size was 3,700 square feet. At 42,000 square feet, Wall 4 accounted for 55 percent of the design-build project's total square footage of 76,000.
"Most project prequalifications that enable your company to bid on a soil nailing project require that you have completed 2,000 soil nails in the last five years," says DeSpain. "This one wall is in excess of that requirement."
Soil conditions were mostly moderate with some areas proving more difficult, which allowed UMA to concentrate its efforts on the sheer size of Wall 4. A large portion of the wall was constructed in a low-quality decomposed granite, which is typical in this part of North Carolina. The remainder was a Piedmont soil, which is a reddish alluvial soil with silt and clay.
"This soil type has some cohesion so when you drill in it, it generally wants to stay open," says DeSpain, noting that UMA has drilled in challenging soil conditions ranging from glacial till to compressed seashells. "We faced challenges trying to keep the holes open in the fracture rock, but it wasn't overly difficult due to the experience of our team and the specially selected drilling and grouting equipment for the project."
Working in lifts
To manage walls that were, in places, greater than 30 feet, UMA worked in lifts. Flatiron handled excavation and the cast-in-place concrete wall, which required UMA to work between its crews for most of the project. Flatiron's first step was to cut the hill down 30 feet to reach the road base with a fleet of four Komatsu excavators and 18 articulated loaders. This mass excavation ultimately exposed Wall 4. UMA's drilling crew worked the wall from one side to the other. Each lift the excavation crew cut out provided a successively lower working platform for the drilling crew.
UMA completed most of Wall 4 with a single drilling rig – a Casagrande C7, one of the largest soil nail rigs on the market. The supporting equipment included concrete pumps, forklifts, grout plants and a water truck. Despite having a single crawler drilling rig doing the work, UMA's crew kept pace with Flatiron's excavation team.
A balance was required to work in between Flatiron's crews. The excavation crew, hindered by wet weather and cold temperatures, persevered to provide UMA with as much access as conditions permitted. The cast-in-place wall crew, on the other hand, required more time to handle formwork, pour concrete, wait for it to cure, and remove the formwork due to the sheer magnitude of this enormous wall.
Using a single rig on this massive wall was intentional, according to DeSpain. "We designed the wall around the 30-foot stroke of the machine," he says, noting that this simplified the operation by allowing the operator to work alone without support from others. "There were days where he was drilling 100 soil nails in a day by himself."
UMA bought the Casagrande C7 Drilling Rig specifically for the Greensboro Western Loop project. It was the first of two C7s that UMA has purchased. "We felt that it was appropriate to buy a new machine because of the size and the length of the project," DeSpain says. "We basically had one crew on the entire project for two years moving from wall to wall."
More than 2,000 nails used
It took more than 2,000 soil nails to complete Wall 4. The length ranged from 15 to 50 feet long, although the vast majority were 30 feet. The C7's 30-foot stroke allowed UMA to drill most holes with a single stroke. A chevron bit was used to drill and air was used to extract the cuttings, leaving an open six-inch-diameter bore hole.
The rig has no carousel to hold additional drill rods so deeper holes required the support of an EZ Spot UR grapple mounted on a mini excavator. The C7 would drill the 30-foot-hole and the grapple was used to set another drill rod to accommodate the additional depth.
UMA used approximately 61,000 linear feet of Grade 75 epoxy-coated threaded bar. Temporary casing was required in areas with collapsing soil and rock, but that was only about 1,400 linear feet. Of the roughly 61,000 linear feet of bar installed, about 5,500 linear feet was in rock and the remainder in soil.
Almost 800 tons of Type I/II cement was mixed on site with a Colcrete Grout plant. Aiming for a 1.85 specific gravity, a mud balance was used to measure the specific gravity of the grout and ensure the proper mix, which included Type I/II Portland Cement, water and admixtures. Once the tooling was extracted, the hole was filled to capacity with grout pumped through a tremie tube, monitoring volume via a magnetic flow meter.
Once the grout emerged from the hole, UMA's crew inserted the bar. Most of the soil nails were anchored by pure friction with the soil. Those in decomposed granite areas were bonded to the rock.
UMA's engineers determined that five-foot horizontal by five-foot vertical spacing was the most cost-effective means to support the soils and critical structures behind Wall 4. The anchor pattern is based on several factors, according to DeSpain. "It's a combination of the soil properties such as friction angle of the soil and the surcharge loading that's above the wall," he explains. The surcharge is the outward force exerted against the wall face by the weight of anything that sits above it.
The length of the soil nails is partly determined by the failure plane behind the wall, which is the assumed location at which the global stability of the structure could fail. "The nail should be installed past the failure plane to bring the factor of safety up to the FHWA-required 1.5," DeSpain says. The friction angle determines the internal shear-stress relationship between the individual soil particles; a higher friction angle generally requires less nail length to meet the factor of safety.
Applying shotcrete facing
UMA's next step was to install a four-inch-thick temporary shotcrete facing. Steel bearing plates were installed over the head of each soil nail while the shotcrete was still wet. That was secured with a bevel washer and hex nut. The corners of the plates had five-inch Nelson studs, equally spaced to transfer the cast-in-place load to the soil nails.
The four-inch-thick, 4,000-psi shotcrete wall was strong enough to hold the wall in place until the final cast-in-place wall was built in accordance with FHWA guidelines. "The shotcrete behind the cast-in-place facing is ancillary to this type of design," DeSpain says. "The temporary shotcrete isn't necessary to the final design of the wall – in this case it was a means to facilitate Flatiron's cast-in-place pour."
Flatiron's cast-in-place crew took over at this point. They tied rebar cages to the Nelson Studs and assembled formwork over the shotcrete face. A 12-inch-thick concrete wall was then poured between the two to complete the finished wall.
This wall is what motorists will see when driving along the Western Loop, according to DeSpain. "The cast-in-place wall is like an aesthetic finish," he explains." It basically finishes the wall."
Unlike some walls UMA has designed and built with sculpted shotcrete, the finish of Wall 4 was specifically selected to complement the proposed sound barrier walls to bring an aesthetically pleasing view to an otherwise lackluster means of earth retention.
Production soared because UMA assigned a large crew, "There were only four people assigned to the other walls on the project, says DeSpain. "We added more personnel on Wall 4 to not only deal with the size of this wall, but also to increase our productivity."
UMA's production approach was to create repetition and eliminate uncertainty to the greatest extent possible," according to DeSpain. He says, "We asked, how can we design the wall to be built in a way that is a repetitive process and can be constructed faster? We wanted to keep the bar and hole sizes consistent to avoid having to cut anything on site."
UMA's focus was to make sure crews could seamlessly select the appropriate materials, set them in place, and move on as effortlessly as possible.
Brian M. Fraley is president of Fraley Construction Marketing.