Best practices for managing fluids and filters in heavy equipment
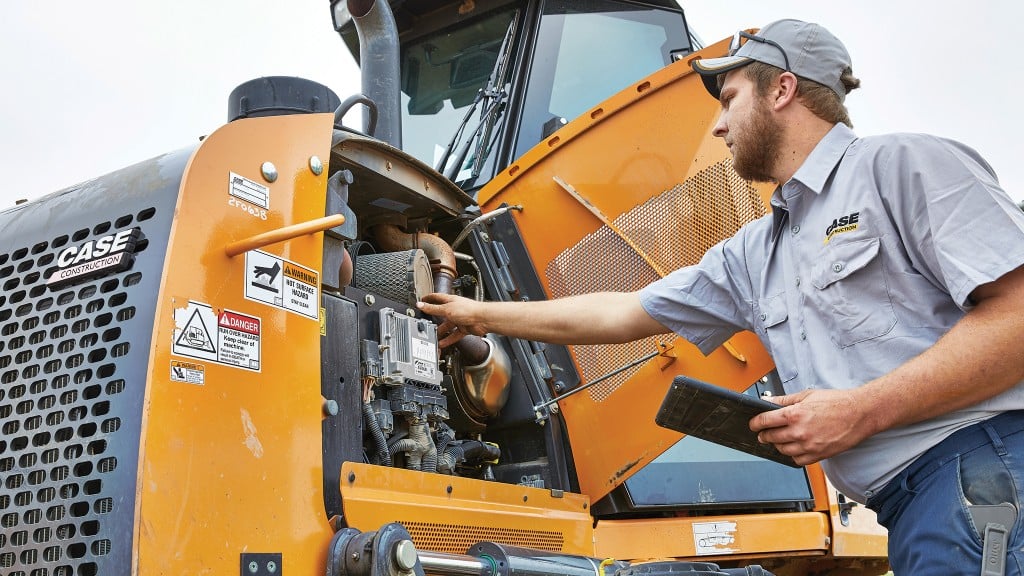
Every piece of heavy equipment powered by a diesel engine has one thing in common: it's full of fluids, and those fluids are integral to the machine's operation. Fuel, oil, hydraulics - all of these fluids need to be managed and maintained effectively to keep equipment up and running.
Having a collection of best practices that ensure an equipment owner's maintenance program keeps fluid and filter management in mind is important, according to experts from CASE Construction Equipment.
"We've all heard it - engine oil is engine oil, hydraulic fluid is hydraulic fluid, and so on. Nothing could be further from the truth, especially today," said Reece Hill, manager of product and service marketing for construction aftermarket solutions with CASE. "Each piece of equipment in your fleet is an investment of tens to hundreds of thousands of dollars into your operation and the fluids and filters you use is a small investment that keeps that big investment moving."
Brent Battaglia, sales leader for construction aftermarket solutions, said that the way in which heavy equipment operates is unique in the level of power in use at any given time, and the fluid and filter selection must be done with that in mind.
"There's much more stress and wear being put on the engine, the fluids, the filters and the machine as a whole, so using filters or fluids from automotive or trucking is not interchangeable," Battaglia said. "They will wear out more quickly, affecting performance. They can also cause damage to the machine and its components. We can not emphasize this enough - use fluids and filters specifically formulated and designed for heavy equipment."
Without ensuring that proper usage, key equipment parts - bearings, bushings, chains and more - can fail early, leading to expensive downtime and reduced productivity.
One simple way to monitor the health of critical fluids is a time-tested method: the eye test. Daily maintenance checks on your equipment can provide good information about the condition of fluids and filtration, Hill said.
"We highly recommend that everybody does their daily operational checks, their pre- and post-operation checks - this Is going to be your chance to identify any issues before they become a downtime event," he said. "You may identify broken hoses, damaged filters, pooled fluids - whatever it might be, identifying those up front and notifying your fleet management staff or local CASE dealer is a good step toward keeping that machine up and running."
It's also a good idea during daily checks to review fluid levels. Hill said hydraulic oil, engine oil and coolant levels should be reviewed daily, and if there are any significant changes, investigate the cause. Keeping fluids at their proper levels is key for equipment health.
"Hydraulic fluid levels and coolant levels need to be kept up to their full marks. It's important that hydraulic and coolant systems run at capacity, because introduction of oxygen into those systems can lead to further damage," Hill said.
The formulation of fluids is a point to consider when choosing the type to use, Battaglia noted. Synthetic oil is becoming a popular choice, for good reason.
"Synthetic oil costs more upfront, but the advantages it provides are significant. First of all, it allows for easier storage. It also provides better protection during extreme or hot temperatures," Battaglia said. "It doesn't matter if you're in upper Canada in the middle of winter, or if you're in Texas in the middle of summer. Additionally, it extends service life - conventional oil should be changed around every 300 hours while synthetic can last up to 500 hours. This equals better protection and less downtime."
One question that is often put to service professionals is regarding service intervals, and how strictly they should be followed. Battaglia said that properly scheduled fluid and filter maintenance should be adhered to as closely as possible.
"Just like you do with an oil change or tire rotation in your car, do them on schedule, as recommended in your manual. This helps to ensure the productivity and health of your equipment and makes sure it lasts longer," he said. "This is easier than ever with our new SiteWatch telematics. It helps you keep track of engine hours and service intervals, and you and your dealer can send and receive alerts so you can stay ahead of maintenance and schedule it during your downtime."
A variety of factors can affect fluids even if they don't seem to have any issues. Hydraulic oils, for example, may absorb moisture in some climates, causing contamination in all of the systems that hydraulic oil runs through, Battaglia noted. Filter changes at those scheduled intervals are key as well, because of their role in removing contamination.
Formulation changes in critical fluids are frequent, especially as emissions requirements change and move forward. One area that has seen many changes recently is that of coolants, Hill noted. A growing interest in organic additive technology, or OAT, coolants is one owners and mechanics should be aware of.
"The primary benefit of OAT is increased protection and better performance. If your machine was factory-filled with OAT there will be a decal near the fill point indicating the use of OAT as well as its brand or formulation," Battaglia said.
Knowing whether a machine has been filled with OAT coolant is very important, because blending conventional coolants with OAT can cause gelling in the system.
Battaglia said that if a change is desired, the system needs to be flushed three times before adding a new coolant.
If owners are curious about the performance of their critical fluids, fluid analysis can provide key insights into the condition of the fluid as well as a snapshot of potential problems, Battaglia noted. It is a simple process for owners, especially as many dealers, including CASE, offer testing kits that can be sent in for analysis.
"The test identifies the overall condition of the fluid, plus any contaminants. The reports give you a heads-up on any particular problems, such as ineffective air filtration or deteriorating bearings. One sample is a snapshot in time, but the real value is trending - doing it repeatedly," Battaglia said. "You can establish a trend, then look at trend analysis over time. For engine oil, we recommend analysis every 250 hours; for hydraulic oil, we suggest every 500 hours; and for coolant, we suggest doing it annually."
Results are generally received within 24 hours, providing troubleshooting recommendations and severe concerns. The overall benefit long-term is maintenance or improvement in resale value - the trend lines detail the life of the machine, maintenance over time and the condition the machine is in, Battaglia noted.
The best way to ensure a good overall fluid and filter maintenance program is to work with your dealer, Hill said. Dealers can be part of the fleet management process for owners and ensure that maintenance is done right, costs are predictable, and the owner understands fully the total cost of operations for each machine.