Mechanical engineering solutions from Built Robotics, Ammann, and Herrenknecht AG nominated for bauma Innovation Award
Three systems vie to win bauma’s 2022 Mechanical Engineering Innovation Award
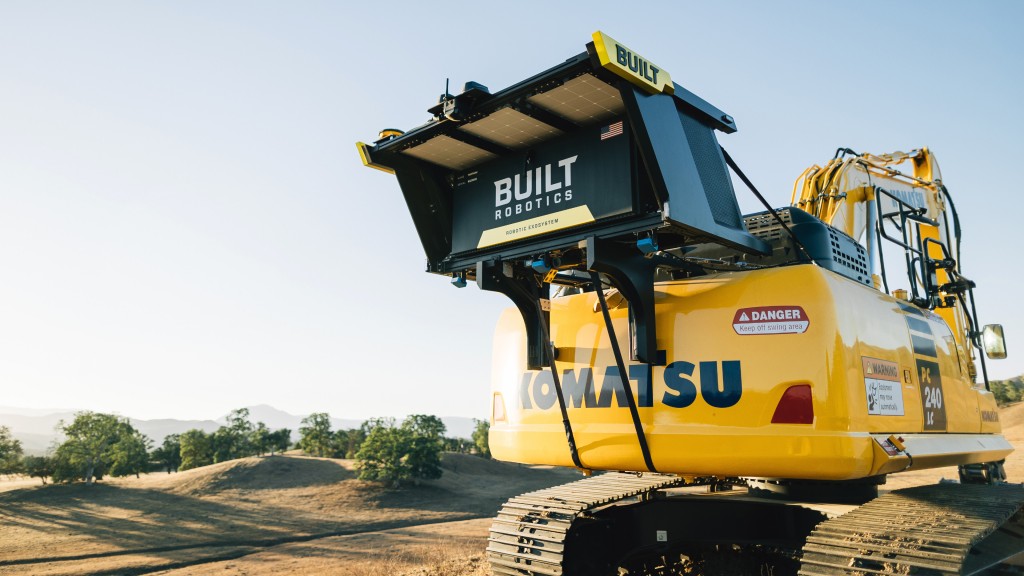
The mechanical engineering category of bauma's 2022 Innovation Award focuses on mobile and stationary systems used in the construction industry, the building trade, the building materials industry, and in mining. The nominees include Built Robotics' Exosystem technology that turns an excavator into a fully autonomous trenching robot; Ammann's eAPX 68/95 3D vibratory compactor that can move in an arc, circle, or turn on the spot; and Herrenknecht AG's continuous tunnelling process for tunnel infrastructure in common soft ground formations with or without water-bearing layers.
Built Robotics' autonomous trenching robot upgrade for excavators
Built Robotics' Exosystem is an aftermarket upgrade that transforms any excavator into an autonomous trenching robot.
Noah Ready-Campbell, the founder and CEO of Built Robotics, says that the Exosystem brings autonomous technology right to the contractor.
Features of Built Robotics' Exosystem technology
The Exosystem aftermarket upgrade features an eight-layer safety system with hardware to help contractors autonomously dig trenches in various soils, elevations, and conditions.
Using sensors and software, the Exosystem helps contractors complete jobs and infrastructure projects faster. Robotic operation of heavy equipment reduces fuel consumption and increases the longevity of equipment. Autonomous digging helps create fewer errors and less re-work leading to reduced waste and delay on job sites.
Built Robotics' autonomous trenching solution installs in less than a day
The Exosystem delivers a reliable solution for autonomous trenching, and can be installed and calibrated on an excavator in less than a day. Contractors can rent Exosystems as standalone units to install on their fleet of equipment, or they can lease pre-upgraded excavators from Built Robotics directly.
In bringing widespread autonomy to construction sites across the globe, Built Robotics says it aims to address critical issues in the built environment through technology. With a growing need for utilities and other buried infrastructure in energy, housing, environment, and clean energy, trenching has proven an important application of autonomy for construction partners.
Ammann APX 68/95 3D vibratory compactor
The Ammann eAPX 68/95 3D vibratory compactor delivers more movement options compared to conventional vibratory plates. Ammann says that this battery-powered plate is the first vibratory compactor on the market that can go in an arc, circle, or turn on the spot.
Vibratory plate design is versatile for applications in tight spaces
The eAPX 68/95 has a low operating height of 700 mm. That height and the machine's ability to move in all directions make it an ideal fit for trench applications, especially those with support systems and cross braces.
Underneath the hood are four working shafts in an X shape that combine with a curved base plate to provide the 620 kg compactor with the ability to go in an arc, circle, or turn on the spot.
A remote-control unit enables the operator to precisely control the eAPX 68/95 at a safe distance. The operator can steer the eAPX 68/95 along straight lines and in hard-to-reach spots.
Ammann eAPX 68/95 vibratory plate drive has no hydraulics, operating fluids, or gears
Four battery-powered electric motors enable the machine to work in applications usually off-limits to combustible engines, including indoors and enclosed spaces.
The compactor can run continuously for approximately 80 minutes before recharging is needed, and recharging only takes 30 minutes. The eAPX 68/95 utilizes lithium iron phosphate (LFP) batteries which are not susceptible to high temperatures, overcharging, and mechanical damage.
The drive requires little maintenance as it has no hydraulics, operating fluids, or gears. The low wear-and-tear, elimination of fluids, and zero emissions make this a sustainable solution that delivers maneuverability and performance.
Herrenknecht AG's continuous tunnelling process
Herrenknecht AG has a new continuous tunnelling process for tunnel infrastructure in common soft ground formations with or without water-bearing layers. Using the latest technology, the continuous tunnelling process leads to a significant reduction in construction time for longer sections of tunnel.
Mechanized tunnelling with shield machines in soft ground has always been a stop-and-go sequential process. Each excavation stroke is followed by the ring-building sequence. The excavation has to pause ,and the subsequent driving cycle is only started when the next ring segment has been completely installed. The interruptions to tunnel advancement in soft ground caused by these sequential operations costs time over long distances.
A continuous tunnelling process, during which the machine can continue excavation while the lining rings are installed, can contribute to considerable savings in construction time – Herrenknecht engineers has designed this continuous tunnelling process.
How continuous tunnelling works
In continuous tunnelling, thrust cylinders that push the machine forward during the advance take over the force share of those cylinders that are retracted for ring building.
To ensure that the machine reliably maintains course under these conditions, the centre of thrust resulting from the combined driving forces of the applied thrust cylinders must remain unchanged in its position. At the heart of continuous tunnelling is computer systems and process-specific software programs that can calculate the necessary pressures in the thrust cylinders. It ensures that the operator can control the tunnel boring machine along the specified alignment as before.
Continuous tunnelling centre of thrust system maintains alignment efficiently
During continuous advance tunnelling, the operator no longer controls the pressures in the thrust cylinders manually using rotary controls (potentiometers) on the control panel. For this purpose, Herrenknecht has developed the centre of thrust (CoT) system, which helps the operator control the machine. It consists of a display panel that shows the operator the current position of the centre of pressure and they can select the desired position of the centre of thrust. The corresponding control of the thrust cylinders is handled by the algorithms in the computer system. Compared to manual control by potentiometers, the CoT can maintain the specified alignment more efficiently.
Continuous tunnelling is faster compared to discontinuous tunnelling
With continuous tunnelling, an increase in performance of up to a factor of 1.6 can be achieved compared to discontinuous tunnelling. This can lead to a significant reduction in construction time for long tunnels, and Herrenknecht says its solution can be used on all machine types in soft ground.
The continuous tunnelling method is being used in the major High Speed 2 project – a new rail link between London and Birmingham in the U.K.
bauma Innovation Award categories
Additional Innovation Awards will be presented in the following categories:
Company info
1125 SW 101St Road
Davie, FL
US, 33324
Website:
ammann-group.com/en/home
Phone number:
954-493-0010