CO2 reduction technologies from Liebherr, carbonauten, and Benninghoven nominated for bauma Innovation Award
Three technologies vie to win bauma’s 2022 Climate Protection Innovation Award
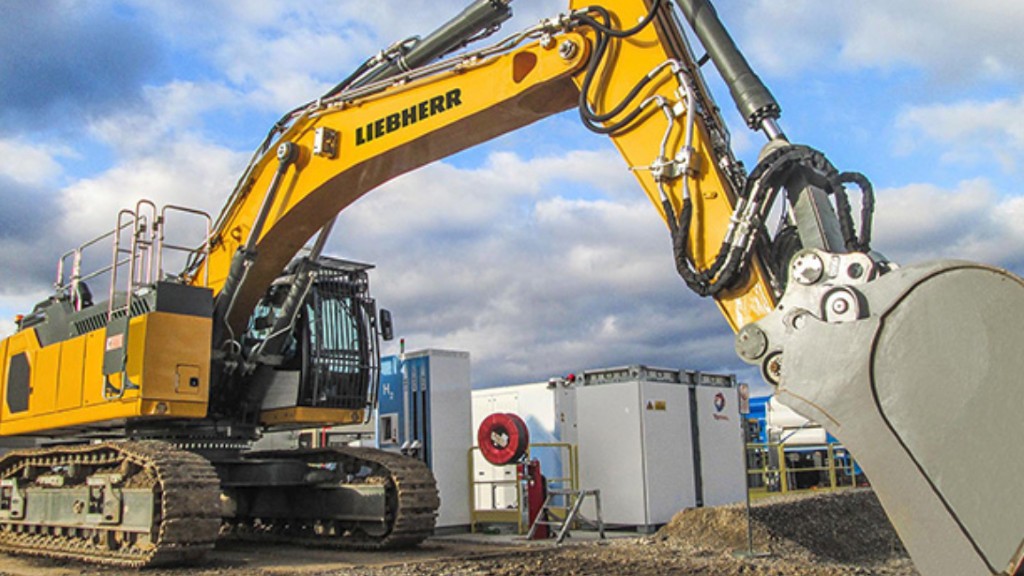
The bauma Innovation Award 2022 in the Climate Protection category features three technologies that enable energy efficiency, sustainability, resource conservation, life cycle assessment, and alternative drives and fuels. The award also takes into account the degree of innovation, the benefit for the user, and the economic potential of the technology. Liebherr France SAS was nominated for its hydrogen engine crawler excavator, carbonauten was nominated for its CO2-reducing building materials, and Benninghoven was nominated for its system that reduces the greenhouse gas emissions from asphalt mixing plants.
Liebherr's R 9H2 hydrogen crawler excavator
Liebherr is working on alternative drive technologies for different product lines to help reduce emissions. One of these solutions is hydrogen-powered engines. At bauma 2022, Liebherr will debut a crawler excavator, developed by Liebherr-France SAS in Colmar, equipped with an integrated hydrogen combustion engine. The H966 engine was developed by Liebherr Machines Bulle SA in Switzerland.
Liebherr's R 9H2 delivers a significant reduction in emissions
The H2 drive in the crawler excavator does not require a permanent energy supply and generates low NOx and CO2 emissions. Depending on how emissions are measured, and whether the entire life cycle of the machine is taken into account, the hydrogen combustion engine reduces CO2 emissions by almost 100 percent in day-to-day operations, or by 70 percent, for the entire life cycle of the machine, from manufacturing to its end of life.
Liebherr's H966 hydrogen engine is desgined for heavy-duty applications
The first Liebherr hydrogen engine, the H966, is designed for both demonstration and field trials and is based on an intake manifold injection technology (also known as PFI). The results of field trials favour the potential of hydrogen propulsion for off-road applications.
Liebherr is working on further hydrogen-based drive technologies, such as H2 direct injection. H2 direct injection enables a higher power density than H2 intake manifold injection and is ideal for heavy-duty applications in construction and mining.
Liebherr's hydrogen crawler excavator is designed to match the performance of its diesel-powered counterpart
The R 9H2's design is based on the current and future generation of Liebherr crawler excavators, offering comfortable and efficient operation. The excavator reaches the same overall performance as its diesel engine counterpart in terms of power output, engine dynamics, and response. Suitable for extreme temperatures, shock, and dust-intensive site operations, the R 92H will be able to operate in earthmoving and quarrying applications alongside conventional excavators. The only difference is how the machine is refuelled. Fast and safe refuelling is enabled through infrared communication between the excavator and the refuelling station, where users benefit from the standard high-speed protocol.
"The tests carried out in Colmar were extremely convincing," says Henrik Weitze, project manager at Liebherr-France SAS. "This technology promises many advantages for us in the future, especially in the most challenging applications."
carbonauten's negative CO2 building materials
carbonauten GmbH believes that CO2 is part of the solution to reach climate targets and reduce emissions. carbonauten was founded by Torsten Becker and Christoph Hiemer in 2017, and their vision is to bind CO2 in biochar over the long term and use it to create new materials. These materials cause no further damage to the environment.
Waste materials from range of industries are transformed into reusable biocarbon materials
The achieve this goal, carbonauten has developed a system for industries, companies, and municipalities. In the company's negative CO2 factories, woody, lumpy, dry, and biogenic residual and problem materials (such as damaged wood, sawmill residues, screen overflows, or food and press residues) are carbonized into biocarbon materials. The biocarbon materials store the equivalent of up to 3.3 tons of CO2 per ton. They are then refined with various binders to form carbonauten's NET (negative emission technology) materials.
carbonauten NET materials used to create asphalt, concrete, and more
The carbonauten NET materials are used to produce biostimulants, as well as plastic products and building materials. Examples of end products include films, asphalt, concrete, plaster, insulation, and plastics of all kinds. carbonauten says that far more energy is generated during the carbonization than the process requires. The excess energy can then be fed into the heat or power grid or can be used to produce hydrogen.
carbonauten's solution is decentralized, scalable, and quick to set up
The negative CO2 factories can be built at decentralized locations around the world to create local circular economies. Because the costs of commissioning and maintaining the facilities are low, ecological benefits go hand in hand with economic potential. As more CO2 is sequestered, more products are produced from carbonauten NET materials.
The first negative-CO2 facility starts production in Germany this fall
The first negative CO2 factory in Eberswalde, Brandenburg (Germany), has been established with ForestFinance Capital GmbH as the investor. It is scheduled to start production of engineered biocarbon materials in the fourth quarter of 2022. Additional locations in Germany, Spain, South America, the U.S., Indonesia, and China are in the planning stages.
Benninghoven's REVOC recycling system reduces asphalt mixing plant emissions
Benninghoven's REVOC system is a technology for reducing the output of greenhouse gases from asphalt mixing plants. In addition to reducing CO2, it can reduce total carbon emissions by as much as 50 percent. The recycling system can meet or even stay below increasingly stringent emissions limits in asphalt production.
REVOC reduces emissions while raising the recycling rate by up to 60 percent
Reclaimed asphalt can already be added to the production process using reliable cold and hot recycling technologies. This, however, results in higher total carbon emissions (Ctot). When reclaimed asphalt is heated, part of the Ctot concentration volatilizes from the bitumen in the recycled material. Ctot has a higher greenhouse gas potential than CO2 and is hazardous to health in higher concentrations. The higher the recycling rate, however, the less fresh bitumen is required and the lower the carbon footprint. Increasing the recycled material from 40 percent to 60 percent alone can save approximately 440 tons of CO2 per year.
In the past, it was practically impossible to resolve the conflict between meeting high recycling rates for reclaimed asphalt while reducing emissions. Benninghoven's REVOC system reduces Ctot emissions by up to 50 percent while implementing higher recycling rates of up to 60 percent.
REVOC provides energy-efficient thermal processing
The REVOC system extracts the emissions directly where they are generated, primarily from the mixer in the asphalt plant, where heated minerals, recycling material, and bitumen come together to make fresh asphalt. The vapours produced during the mixing process have increased Ctot concentrations and are moved to the REVOC system for thermal processing.
The REVOC system enables a high level of energy efficiency by using the energy that is generated for drying and heating the virgin mineral (primary function) for thermal processing of the total carbons (secondary function). According to Benninghoven, data from multiple REVOC systems shows that the technology is already successful in applications.
Existing mixing plants can be retrofitted with REVOC
The REVOC system can upgrade existing mixing plants to meet stricter environmental requirements set out by varous governments. The REVOC system can be retrofitted onto asphalt mixing plants already in operation – which is essential for plant owners as the lifespan of asphalt mixing plants is between 20 and 30 years.
bauma Innovation Award categories
Additional Innovation Awards will be presented in the following categories:
Company info
Mossel,
DE,
Website:
benninghoven.com/index.php?Itemid=26&id=12&option=com_content&task=view
1015 Sutton Drive
Burlington, ON
CA, L7L 5Z8
Website:
liebherr.com/en/can/about-liebherr/liebherr-worldwide/canada/liebherr-in-canada.html