CDE collaborates with Granite on water-efficient wash plant in Utah
The new 550-ton-per-hour wet processing facility was designed to work in the unique Salt Lake City area
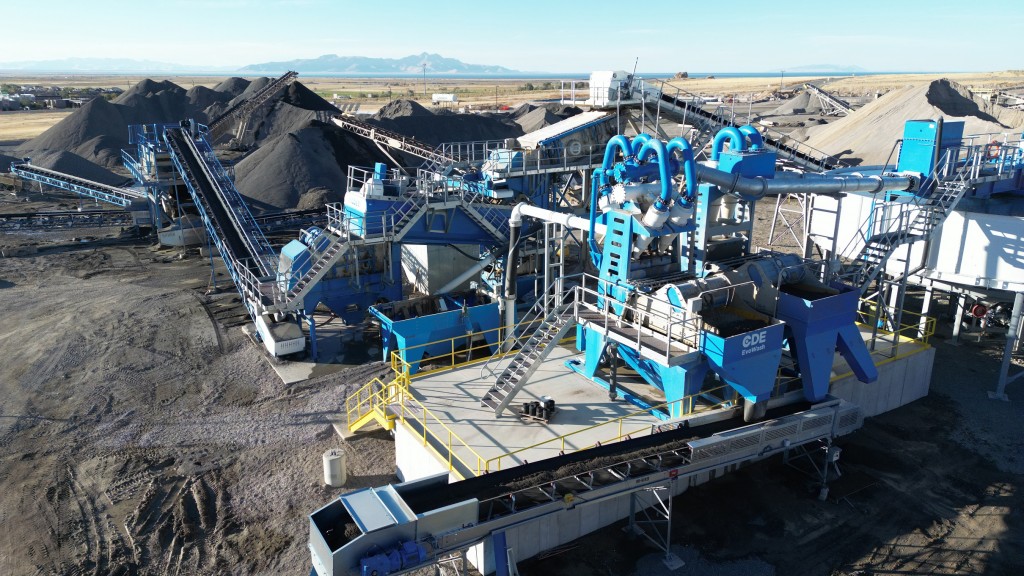
CDE has built a 550-ton-per-hour (tph) plant in Utah for Granite. It is designed to work efficiently while taking into consideration the environmental concerns of the surrounding area. One of the biggest challenges with the Coyote Pit site is water management. In the dry climate of Salt Lake City, water is a precious commodity, making efficient usage crucial.
CDE has extensive experience designing and engineering sand and aggregate wet processing solutions for the natural minerals processing sectors, and after a thorough consultation process, Granite decided to collaborate with CDE on this large plant.
Wash plant needed to meet increased aggregate demand
The investment in the new wet processing facility came as Granite aims to increase its aggregate supply to meet the rising demand in the Wasatch Front region, including the Greater Salt Lake City area. The Salt Lake City region is experiencing rapid economic development and infrastructure expansion driven by population growth as well as the coming 2034 Winter Olympics, which will require significant infrastructure investments.
As a company involved in both construction and materials supply, Granite sought to increase the volume of material it could supply to the market to affirm its position as a major sand and aggregates supplier in the Greater Salt Lake City area.
Building solid business foundations
After initial discussions, CDE showcased its solutions and technical capabilities through site visits to plants in Texas where the relationship continued to develop. During CONEXPO 2023, the conceptual development discussions continued, and an agreement was signed by late August 2023.
The Granite team also visited CDE's manufacturing base in Northern Ireland to tour the facility, inspect the quality of the equipment and deep dive into the project plant which provided reassurance and cemented their belief that CDE was the right partner.
"We were impressed by CDE's technology from the get-go, but after seeing it in action at the reference sites in Texas, attending CDE's Open House event with Calgary Aggregate Recycling in Alberta, and in its manufacturing facility, we knew we had made the right choice," says Ric Skinner, manager at Granite. "CDE's approach, technology and commitment to providing the most optimal solution to meet our business needs all played a critical role in cementing this partnership."
"Granite's decision was solidified after visiting several of our plants to see the technology in action," adds CDE's business development manager Ryan O'Loan. "Organizing these visits certified our commitment to going the extra mile for our customers, along with our transparency in showing past projects, which played a critical role in securing this partnership."
A complex solution delivered quickly
The urgency of the project became a top priority in late 2023, with Granite needing to have material on the ground by May of 2024. Granite had a location close to the city and a market starved of aggregate, says the company. They needed a high tonnage solution that met its complex water management and mud handling requirements, all to be delivered in a fast timeframe.
"After building a solid relationship, and showcasing our innovative technologies, the team at Granite knew they could trust CDE," says O'Loan. "We were able to guarantee tonnage, quality, and delivery with our performance statement and commercial terms."
The balance between the limited water availability and the need for high-specification sand and aggregates — both of which require washing — presents a unique challenge. The 550 tph plant involves CDE's AggMax scrubbing and classification system, EvoWash sand wash system, AquaCycle thickener primary stage water management, AquaStore water tank, and filter press sludge dewatering system.
The environmental considerations require a solution that firstly, washes and scrubs the materials as efficiently as possible and secondly, retains as much water within a closed-loop system, significantly reducing the need to source additional water from the environment. This is why CDE has integrated its filter press and AquaCycle thickener technologies. When these two systems work together, they recycle up to 95 percent of the process water for immediate re-use in the system, in turn significantly reducing the freshwater consumption. To date, the plant has only required 11,000 gallons per hour of freshwater, demonstrating Granite's commitments to sustainability and preserving the area's water supply.
A consistent and reliable supply of sand and aggregates
This solution, which typically loses about 20 percent as tailings, allows Granite to produce over 300 tons per hour of washed concrete aggregate products, either for internal use in its construction projects, or as saleable products. In addition to the filter cake, with CDE's technology, Granite is producing a C33 washed concrete sand, #67 washed rock, 1.5-inch washed rock, 0.375-inch washed chips, and 0.25-inch washed chips.
To date, Granite has produced over 410,000 tons of sellable material which are serving construction projects in Salt Lake City and the wider Wasatch Front region, enhancing Granite's supply chain efficiency.
"This plant is everything we could have wanted and more," says Stormy Watne, plant manager at Granite. "CDE have delivered exactly what they set out to. We had a number of challenges facing us, such as the commissioning deadline, the need for efficient water management and mud handling capabilities, but at every step of the way CDE reassured us and demonstrated that their solution is suited to our objectives."
"From the outset we knew that this would be a meaningful and impactful project," says O'Loan. "This plant was complex and took meticulous planning and collaboration to see it successfully operate. Personal relationships and trust were pivotal throughout every stage of the process. We're proud to supply a solution that ensures Granite can provide a consistent and reliable supply of sand and aggregates for use in the local construction market.